Guia Completo sobre Manutenção e Calibração de Equipamentos Essenciais
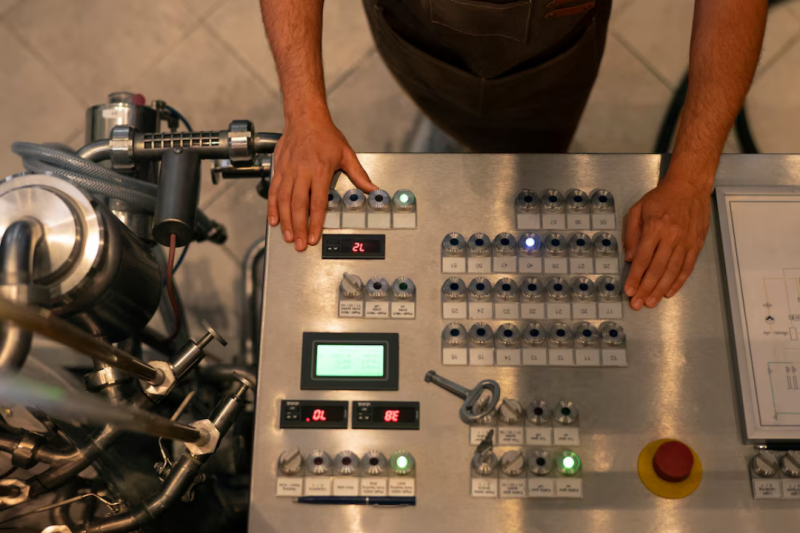
Por: Cláudio - 20 de Março de 2025
A manutenção e calibração de equipamentos são práticas essenciais em diversos setores, garantindo a eficiência e a segurança operacional. Através de métodos corretos, é possível prolongar a vida útil dos equipamentos e minimizar falhas. Este guia aborda os aspectos mais relevantes para a implementação de um programa eficaz de manutenção e calibração.
Importância da Manutenção em Equipamentos Industriais
A manutenção regular de equipamentos industriais é crucial para assegurar a continuidade das operações e a segurança no ambiente de trabalho. Equipamentos que não passam por cuidados adequados podem apresentar falhas, resultando em paradas inesperadas e prejuízos financeiros significativos.
Além de evitar quebras, a manutenção contribui para a eficiência energética. Equipamentos mal mantidos tendem a consumir mais energia, aumentando os custos operacionais. Através de intervenções regulares, é possível otimizar o desempenho, reduzindo o gasto de recursos e promovendo uma operação mais sustentável.
Outro aspecto importante é a segurança dos colaboradores. Equipamentos em mau estado de funcionamento podem representar riscos significativos, podendo causar acidentes. A manutenção preventiva ajuda a identificar e corrigir problemas antes que eles se tornem perigosos, garantindo um ambiente de trabalho mais seguro.
A prolongação da vida útil dos equipamentos também é um benefício direto da manutenção. Com cuidados adequados, os itens de maquinário podem funcionar de maneira eficaz por longos períodos, garantindo que os investimentos feitos não sejam desperdiçados.
Por fim, a documentação das práticas de manutenção é essencial. Manter registros claros permite que as empresas identifiquem padrões de falhas e desenvolvam estratégias de melhoria contínua. Esse acompanhamento é vital para qualquer plano de gestão de ativos, contribuindo para decisões mais informadas.
Tipos Comuns de Calibração em Equipamentos Técnicos
A calibração de equipamentos técnicos é fundamental para assegurar que os instrumentos funcionem corretamente e com precisão. Existem vários tipos de calibração, cada um destinado a atender diferentes necessidades e tipos de equipamentos.
Um dos tipos mais comuns é a calibração de instrumentos de medição, como multímetros e manômetros. Esses dispositivos são essenciais em diversos setores, incluindo eletricidade e hidráulica. A calibração garante que as medições realizadas sejam precisas, evitando erros que podem levar a falhas de operação.
Outro tipo importante é a calibração de sensores, que são utilizados para monitorar variáveis como temperatura, pressão e umidade. Sensores mal calibrados podem transmitir informações enganosas, impactando a qualidade e segurança dos processos industriais.
A calibração de dispositivos médicos também merece destaque. Equipamentos como respiradores e monitores de sinais vitais precisam ser calibrados com precisão para garantir a segurança dos pacientes em ambientes hospitalares. Uma calibração incorreta pode ter consequências graves para a saúde.
Além disso, a calibração de equipamentos de controle de qualidade é essencial em processos de fabricação. Medidores de calibre, balanças e outros instrumentais são calibrados para garantir que os produtos atendam aos padrões exigidos antes de serem enviados ao mercado.
Por fim, a calibração de máquinas CNC (Controle Numérico Computadorizado) é vital em setores como a usinagem. Esses equipamentos precisam manter alta precisão para garantir que as peças sejam fabricadas conforme as especificações. A calibração regular ajuda a evitar desperdícios e a assegurar que os processos de produção sejam eficientes.
Passo a Passo para Realizar a Manutenção Preventiva
Realizar a manutenção preventiva de equipamentos industriais é um processo sistemático que ajuda a garantir um funcionamento ideal e a evitar falhas.
Abaixo, apresentamos um passo a passo para efetivar essa prática.
1. Planejamento: O primeiro passo é criar um cronograma de manutenção que inclua a frequência com que cada tipo de equipamento deve ser inspecionado e mantido. Esse cronograma deve ser definido com base nas recomendações do fabricante e nas particularidades do ambiente de trabalho.
2. Checklist de Inspeção: Desenvolva uma lista de verificação para cada equipamento, especificando os pontos a serem inspecionados, como sistemas elétricos, mecânicos, conectores, entre outros. Isso ajuda a garantir que nenhuma parte crítica seja negligenciada durante a manutenção.
3. Execução da Manutenção: Com o planejamento e checklist em mãos, inicie a manutenção. Isso pode envolver limpeza, troca de peças desgastadas, lubrificação de partes móveis, e verificação de alinhamentos. É fundamental seguir as diretrizes do fabricante durante este processo.
4. Provas de Funcionamento: Após realizar a manutenção, teste o equipamento para garantir que tudo esteja funcionando corretamente. Verifique se não há ruídos estranhos, acúmulo de vazamentos ou qualquer anomalia que poderia indicar um problema.
5. Documentação: Registre todas as atividades de manutenção realizadas. Isso inclui data, tipo de trabalho executado, peças substituídas e resultados dos testes de funcionamento. A documentação adequada auxilia na criação de um histórico que pode ser útil para futuras manutenções.
6. Análise de Desempenho: Revise regularmente o desempenho dos equipamentos após a manutenção preventiva. Com isso, você poderá identificar tendências e fazer ajustes no cronograma de manutenção, se necessário, para melhorar a eficiência e prevenir falhas futuras.
Sinais de Que Seu Equipamento Precisa de Calibração
Identificar sinais de que um equipamento precisa de calibração é essencial para garantir a precisão das medições e a segurança nos processos. Abaixo estão alguns indicadores comuns que podem sugerir a necessidade de calibração.
1. Inconsistência nas Medições: Se você notar variações significativas e inexplicáveis nas medições realizadas pelo equipamento, isso pode indicar que ele está fora de calibração. Comparar os resultados com padrões conhecidos pode ajudar a confirmar essa dúvida.
2. Sinais de Desgaste: Partes visíveis do equipamento que apresentam desgaste físico, como rachaduras, corrosão ou danos, podem comprometer a precisão. Nesses casos, é essencial verificar a calibração e realizar manutenção corretiva.
3. Mudanças de Ambiente: Equipamentos que operam em ambientes onde ocorrem alterações significativas de temperatura, umidade ou pressão devem ser recalibrados regularmente. Essas mudanças podem afetar o desempenho e a precisão das medições.
4. Erros em Funcionamento: Mensagens de erro ou falhas frequentes durante a operação são sinais claros de que a calibração pode estar comprometida. Verifique os manuais do fabricante para compreender como esses erros estão relacionados à calibração do equipamento.
5. Procedimentos de Calibração Programados: Seguir um cronograma de calibração regular é fundamental. Se um equipamento está além do tempo programado para calibração, é hora de realizar a verificação, independentemente do seu estado aparente.
6. Alterações no Fornecedor: Quando um novo fornecedor de peças ou materiais é introduzido no processo, pode ser necessária uma recalibração. Mudanças na qualidade dos insumos podem impactar diretamente o funcionamento do equipamento.
Benefícios da Manutenção Regular para a Durabilidade dos Equipamentos
Manter um programa de manutenção regular traz inúmeros benefícios que vão além da simples funcionalidade dos equipamentos. Tais benefícios são cruciais para garantir a durabilidade e eficiência a longo prazo.
1. Aumento da Vida Útil: A manutenção regular ajuda a evitar o desgaste excessivo de componentes, resultando em uma vida útil prolongada do equipamento. Com cuidados adequados, equipamentos que poderiam falhar prematuramente poderão operar de maneira eficiente por anos.
2. Redução de Custos com Reparos: Equipamentos bem mantidos tendem a apresentar falhas menos frequentes, diminuindo os gastos com manutenção corretiva e reparos emergenciais. Isso se traduz em economia significativa ao longo do tempo.
3. Melhoria na Eficiência Operacional: A manutenção regular garante que os equipamentos funcionem em suas melhores condições. Isso melhora a eficiência operacional, resultando em maior produtividade e menores tempos de parada.
4. Segurança Aumentada: Manter os equipamentos em boas condições contribui para um ambiente de trabalho mais seguro. A manutenção ajuda a identificar e corrigir problemas potenciais antes que eles causem acidentes, protegendo colaboradores e ativos da empresa.
5. Conformidade com Normativas: Muitos setores exigem que os equipamentos estejam em conformidade com normas de segurança e operacionais. A manutenção regular ajuda a garantir que essas normas sejam atendidas, evitando penalizações e garantindo a confiança dos clientes.
6. Valorização do Investimento: Com a manutenção adequada, o valor de revenda do equipamento pode ser maior. Isso significa que, se houver a necessidade de substituir um equipamento, a empresa pode obter um retorno melhor sobre o investimento inicial.
Ferramentas Indispensáveis para Manutenção e Calibração Eficiente
Para garantir a eficiência nas práticas de manutenção e calibração, é fundamental ter as ferramentas adequadas. Abaixo estão algumas das ferramentas indispensáveis para realizar essas tarefas com eficácia.
1. Multímetro Digital: Essencial para medir tensão, corrente e resistência em circuitos elétricos. Essa ferramenta é indispensável para a calibração de instrumentos elétricos e para diagnosticar problemas em sistemas elétricos.
2. Calibrador de Pressão: Utilizado para verificar e ajustar medidores de pressão, garantindo que os instrumentos forneçam leituras precisas. Esse equipamento é crucial em ambientes industriais onde a pressão é um parâmetro crítico.
3. Termômetro de Precisão: Ferramenta importante para medir a temperatura em diversos processos. Termômetros calibrados e precisos são fundamentais em setores como o farmacêutico e alimentício, onde a temperatura controla qualidade e segurança.
4. Chave de Torque: Usada para apertar parafusos e porcas com um nível de tensão específico. A calibragem de máquinas depende frequentemente da correta aplicação de torque, e a chave de torque ajuda a garantir que as especificações do fabricante sejam atendidas.
5. Nível de Bolha: Ferramenta simples, mas eficiente, para garantir que equipamentos estejam alinhados corretamente. Manter o alinhamento adequado é vital para o funcionamento eficiente dos maquinários.
6. Software de Gestão de Manutenção: Utilize ferramentas digitais para gerenciar manutenções, agendar calibrações e documentar processos. Isso ajuda a manter um registro organizado e a facilitar o acompanhamento das necessidades de manutenção dos equipamentos.
A manutenção e calibração de equipamentos são práticas essenciais para garantir a eficiência e a segurança nas operações industriais. Os benefícios dessas ações se refletem diretamente na durabilidade dos equipamentos, na redução de custos e na otimização do desempenho operacional.
Investir em manutenção regular e utilizar as ferramentas adequadas são passos fundamentais para evitar falhas inesperadas e garantir a precisão nas medições. Ao seguir um planejamento estruturado, é possível prolongar a vida útil dos equipamentos e criar um ambiente de trabalho mais seguro.
Portanto, adote uma abordagem proativa em relação à manutenção e calibração e assegure que seus equipamentos estejam sempre operando em sua melhor capacidade. Essa prática não apenas protege seu investimento, mas também desempenha um papel crucial na eficiência e sucesso a longo prazo de suas operações.