Calibração e Manutenção de Instrumentos de Medição para Precisão Aumentada
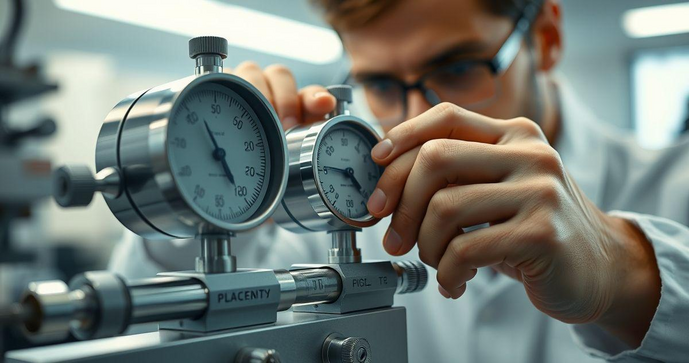
Por: Cláudio - 17 de Abril de 2025
Importância da Calibração de Instrumentos de Medição
A calibração de instrumentos de medição é um processo fundamental que garante a precisão e confiabilidade das medições realizadas em diversas indústrias. Este procedimento consiste em comparar as medições de um instrumento com padrões conhecidos, permitindo ajustes necessários para assegurar que os resultados estejam de acordo com os parâmetros esperados.
Precisão nos Resultados
A principal razão para a calibração é a garantia de precisão. Instrumentos incorretamente calibrados podem gerar dados imprecisos, resultando em decisões falhas e perdas financeiras. Por exemplo, em setores como a farmacêutica, onde a dosagem correta de medicamentos é crucial, a calibração frequente é vital para assegurar a eficácia dos produtos.
Conformidade com Normas
A calibração também é essencial para atender às normas regulatórias. Muitas indústrias são obrigadas a seguir diretrizes rigorosas que exigem a calibração regular de seus instrumentos. O não cumprimento dessas normas pode resultar em penalidades legais e comprometer a qualidade do produto final.
Redução de Perdas e Desperdícios
Instrumentos calibrados adequadamente ajudam a minimizar desperdícios e perdas. Em processos produtivos, a medição precisa garante que as quantidades corretas de materiais sejam utilizadas, evitando excessos ou faltas que podem impactar a eficiência operacional. Este cuidado não apenas melhora a produtividade, mas também contribui para a sustentabilidade, reduzindo o impacto ambiental.
Confiabilidade nas Decisões
Quando as medições são confiáveis, as decisões tomadas pelos gestores são embasadas em dados sólidos. Isso é especialmente importante em setores como a construção civil, onde a precisão nas medições pode impactar diretamente a segurança e a viabilidade financeira dos projetos. Calibrar os instrumentos garante que os engenheiros e arquitetos baseiem suas decisões em informações corretas.
Custo-Benefício
Finalmente, investir em calibração regular pode resultar em economia a longo prazo. A redução de falhas, retrabalhos e desperdícios por conta de medições erradas traz uma economia significativa, que supera os custos envolvidos na calibração dos instrumentos. Portanto, considerar a calibração como um investimento, e não como um custo, pode ajudar as empresas a se tornarem mais competitivas no mercado.
Principais Tipos de Instrumentos que Necessitam de Calibração
Diversos tipos de instrumentos de medição requerem calibração regular para garantir sua precisão e confiabilidade. Conhecer quais são esses instrumentos é fundamental para assegurar que as medições realizadas sejam corretas e atendam aos padrões exigidos em diferentes setores. Os principais tipos incluem:
1. Medidores de Pressão
Os medidores de pressão são amplamente utilizados na indústria para monitorar e controlar processos. A calibração periódica é necessária para garantir que esses instrumentos forneçam leituras exatas, essenciais para a operação segura de equipamentos como caldeiras e compressores.
2. Termômetros
Existem diferentes tipos de termômetros, incluindo digitais e analógicos, utilizados em setores como alimentos, farmacêutico e químico. A precisão da temperatura é crítica para garantir a segurança e a qualidade dos produtos, tornando a calibração uma prática indispensável.
3. Instrumentos de Medição de Nível
Os sensores e medidores de nível são utilizados para detectar e medir a quantidade de líquidos ou sólidos em tanques e silos. A calibração regular desses instrumentos ajuda a evitar transbordamentos e garantir a eficiência no uso dos insumos.
4. Multímetros
Esses dispositivos são usados para medir diferentes grandezas elétricas, como tensão, corrente e resistência. A precisão nas medições elétricas é crítica em aplicações industriais e de manutenção, fazendo com que a calibração seja uma necessidade regular.
5. Balancas de Precisão
Balancas são utilizadas em diversas indústrias para garantir que as quantidades de materiais estejam corretas. A calibração de balanças é essencial, principalmente em setores como farmacêutico e alimentar, onde um erro na pesagem pode resultar em graves consequências.
6. Medidores de Fluxo
Instrumentos que medem o fluxo de líquidos ou gases também precisam de calibração para garantir medições exatas. A precisão neste tipo é essencial em operações industriais para otimizar processos e evitar desperdícios.
7. Espectrômetros
Usados principalmente em laboratórios para análise química e espectroscopia, os espectrômetros devem ser calibrados para garantir que as leituras de compressão e absorção de luz sejam precisas, afetando diretamente a validação de resultados em pesquisas e desenvolvimento.
8. Analisadores de Gases
Esses instrumentos são importantes para a medição de gases em ambientes industriais. A calibração regular assegura a precisão das medições, contribuindo para a segurança e a conformidade com as normas ambientais.
Cada um desses instrumentos desempenha um papel crucial em seus respectivos setores, e a calibração adequada é vital para garantir a precisão e a segurança nas medições realizadas.
Frequência Recomendada para a Calibração
A frequência recomendada para a calibração de instrumentos de medição pode variar de acordo com diversos fatores, incluindo o tipo de instrumento, a utilização e as condições do ambiente em que está operando. Entender essas variáveis é essencial para garantir medições precisas e confiáveis. A seguir, detalhamos as diretrizes gerais sobre a frequência de calibração.
1. Normas e Regulamentos
Em muitos setores, as normas e regulamentos estabelecem a frequência mínima para calibração. Por exemplo, laboratórios credenciados podem ser obrigados a calibrar seus instrumentos mensalmente ou trimestralmente para atender às exigências de organismos reguladores. É importante consultar as diretrizes específicas de cada setor para garantir conformidade.
2. Uso do Instrumento
A frequência de calibração deve ser ajustada conforme a intensidade de uso do instrumento. Equipamentos utilizados com alta frequência ou em ambientes adversos (como temperaturas extremas ou alta umidade) podem exigir calibrações mais frequentes, como mensalmente ou trimestralmente, para manter a precisão.
3. Tipo de Instrumento
Instrumentos mais críticos para a segurança e a qualidade dos produtos, como medidores de pressão e pesos, podem necessitar de calibração a cada seis meses. Já outros instrumentos menos críticos podem exigir calibrações anuais. A avaliação regular dos tipos de instrumentos em utilização ajuda a determinar a frequência mais adequada.
4. Histórico de Desempenho
Acompanhar o histórico de desempenho do instrumento também é importante. Se um instrumento apresentar medições inconsistentes ou falhas frequentes, pode ser necessário aumentar a frequência das calibrações. Registros de medições e a análise de tendências podem ajudar a identificar a necessidade de ajustes.
5. Mudanças no Ambiente de Trabalho
Se o instrumento for transferido para um novo ambiente, a calibração deve ser realizada antes do uso, independentemente da última calibragem. Mudanças na temperatura, pressão ou umidade podem impactar a precisão de medições e, portanto, a calibração é essencial nesse contexto.
6. Recomendação do Fabricante
Os fabricantes frequentemente fornecem recomendações sobre a frequência de calibração para seus produtos. Seguir essas diretrizes é fundamental, pois os fabricantes baseiam suas recomendações em testes e pesquisas. Consultar o manual do usuário ou os documentos técnicos pode fornecer informações valiosas sobre as práticas recomendadas.
7. Uso de Padrões Internos
Empresas podem implementar padrões internos de calibração que vão além das exigências regulatórias. Isso pode incluir intervalos de calibração mais rigorosos e rotinas de manutenção para garantir que a precisão dos instrumentos sempre atenda às expectativas de qualidade e confiança.
Resumindo, a frequência recomendada para a calibração dos instrumentos de medição deve considerar as normas do setor, a intensidade de uso, o tipo de instrumento, as condições do ambiente e as recomendações do fabricante. Realizar calibrações regulares e manter um plano de manutenção é fundamental para garantir a precisão e a confiabilidade das medições.
Métodos e Procedimentos para Calibrar Instrumentos
A calibração de instrumentos de medição é um processo essencial que deve ser realizado seguindo métodos e procedimentos específicos para garantir a precisão das medições. A seguir, apresentamos um guia abrangente sobre os principais métodos e procedimentos utilizados na calibração.
1. Preparação do Instrumento
Antes de iniciar a calibração, é fundamental garantir que o instrumento esteja em boas condições de funcionamento. Isso inclui a limpeza do dispositivo, verificação de danos visíveis e a garantia de que todos os componentes estejam corretamente montados. Documentar o estado inicial do instrumento pode ser útil para referência futura.
2. Seleção de Padrões de Referência
Para realizar a calibração, é necessário utilizar padrões de referência que tenham um nível de precisão conhecido, geralmente rastreáveis a padrões nacionais ou internacionais. A escolha do padrão deve ser feita com base nas especificações do instrumento e nos requisitos da aplicação. Os padrões utilizados devem ter um nível de incerteza menor que o instrumento que está sendo calibrado.
3. Procedimentos de Calibração
O procedimento de calibração varia de acordo com o tipo de instrumento. Exemplos incluem:
- Calibração de Medidores de Pressão: O instrumento é posicionado em um ambiente controlado, e a pressão é aplicada em incrementos. As leituras do instrumento são então comparadas com os valores do padrão de referência.
- Calibração de Termômetros: Coloque o termômetro em um banho de temperatura conhecida, registrando as leituras em diferentes pontos de temperatura e ajustando conforme necessário.
- Calibração de Balancas: Utilize pesos padrões para verificar a precisão da balança em diferentes faixas de peso, realizando os ajustes conforme necessário.
4. Registro de Resultados
Todos os resultados da calibração devem ser documentados de forma organizada. Isso inclui as condições da calibração, os padrões utilizados e qualquer ajuste feito ao instrumento. Registros detalhados são essenciais para garantir a rastreabilidade e a conformidade com normas regulatórias.
5. Ajustes Necessários
Com base nos resultados obtidos, pode ser necessário fazer ajustes no instrumento. Cada tipo de instrumento terá um procedimento específico para ajustar suas configurações. Após realizar os ajustes, é aconselhável repetir a calibração para verificar se as medições agora estão em conformidade com os padrões de referência.
6. Testes de Verificação Pós-Calibração
Após finalizar a calibração e os ajustes, é crucial realizar testes de verificação para assegurar que o instrumento esteja operando corretamente. Isso pode incluir medir novamente em pontos de calibração especificados e comparar os resultados com os padrões de referência.
7. Manutenção e Recalibração
Após a calibração, é importante estabelecer um cronograma de manutenção e recalibração, conforme as diretrizes discutidas anteriormente. A manutenção regular vai ajudar a garantir que o instrumento mantenha sua precisão e que problemas sejam identificados antes de impactar a qualidade das medições.
A calibração apropriada dos instrumentos de medição é vital para garantir resultados confiáveis e precisos. Seguir estes métodos e procedimentos assegurará a eficácia das medições realizadas e a conformidade com as normas exigidas.
Sinais que Indicam Necessidade de Manutenção
Identificar os sinais que indicam a necessidade de manutenção em instrumentos de medição é crucial para garantir a precisão e a confiabilidade das medições. Aqui estão alguns dos principais sinais que podem indicar que um instrumento precisa de manutenção:
1. Leitura Inconsistente
Se um instrumento apresentar leituras inconsistentes ou variar em medições que deveriam ser idênticas, é um indicativo claro de que pode haver um problema. Isso pode sugerir que o instrumentário precisa de calibração ou manutenção para corrigir falhas.
2. Desempenho Abaixo do Esperado
Quando um instrumento não está funcionando tão eficientemente quanto deveria, como demora mais para estabilizar suas medições ou falha em atingir valores esperados, é um sinal de que a manutenção é necessária. Essas falhas podem comprometer a qualidade do trabalho realizado.
3. Sinais Visíveis de Danos
Inspecionar regularmente os instrumentos em busca de sinais visíveis de danos, como rachaduras, corrosão ou peças soltas, é crucial. Qualquer dano físico pode impactar negativamente a precisão, e a manutenção deve ser feita imediatamente para evitar consequências mais graves.
4. Alertas de Erros
Se o instrumento estiver equipado com um sistema de monitoramento, como alarmes ou mensagens de erro, estes devem ser levados a sério. Os avisos em display indicam que o instrumento pode estar fora de especificação e requer manutenção urgente.
5. Mudanças no Ambiente de Operação
Mudanças no ambiente em que o instrumento opera, como alterações nas temperaturas ou umidade, podem afetar seu desempenho. Se as condições ambientais forem alteradas, é recomendável realizar uma verificação e, se necessário, uma manutenção para garantir que o instrumento funcione corretamente.
6. Histórico de Uso Intenso
Instrumentos que são utilizados frequentemente ou que estão expostos a condições extremas, como vibração, poeira ou produtos químicos, podem precisar de manutenção mais frequente. Se um instrumento tiver um histórico de uso intenso, é prudente programar inspeções regulares.
7. Alterações nos Procedimentos Operacionais
Se houver mudanças significativas nos procedimentos operacionais que podem impactar a utilização do instrumento, como novos métodos ou ambientes de uso, isso pode requerer uma revisão nas condições de manutenção. Ajustes podem ser necessários para assegurar que o instrumento continue a atender às exigências.
8. Feedback da Equipe Operacional
A equipe que utiliza os instrumentos pode fornecer feedback valioso. Se os operadores perceberem que um instrumento não está funcionando como esperado ou relatar dificuldades na utilização, uma manutenção deve ser agendada para investigar e resolver os problemas relatados.
Reconhecer esses sinais e agir rapidamente pode evitar problemas maiores e garantir que os instrumentos de medição permaneçam precisos e funcionais. A manutenção preventiva baseada na identificação desses sinais ajuda a prolongar a vida útil dos equipamentos e melhorar a qualidade das medições.
Benefícios da Manutenção Regular de Instrumentos de Medição
A manutenção regular de instrumentos de medição é essencial para garantir sua precisão e confiabilidade. Diversas vantagens estão associadas a práticas de manutenção adequadas, beneficiando tanto as operações quanto a qualidade dos produtos. A seguir, destacamos os principais benefícios da manutenção regular:
1. Aumento da Precisão
A manutenção periódica garante que os instrumentos operem com alta precisão, evitando medições incorretas. Isso é particularmente importante em setores críticos onde a precisão dos dados pode impactar a qualidade do produto e a segurança dos processos.
2. Redução de Custos
Investir em manutenção regular pode resultar em economia a longo prazo. Instrumentos bem mantidos tendem a apresentar menos falhas e, portanto, requerem menos reparos dispendiosos. Além disso, a redução de erros nas medições minimiza o retrabalho e o desperdício de materiais, otimizando os custos operacionais.
3. Prolongamento da Vida Útil dos Equipamentos
A manutenção adequada não apenas mantém a precisão, mas também ajuda a prolongar a vida útil dos instrumentos. Cuidados regulares evitam desgastes excessivos, permitindo que os equipamentos permaneçam em uso por mais tempo, o que é especialmente importante em investimentos significativos.
4. Melhor Conformidade com Normas Regulatórias
Setores industriais muitas vezes têm que cumprir regulamentações rigorosas. A manutenção regular assegura que os instrumentos estejam dentro dos padrões exigidos, evitando penalidades legais e mantendo a reputação da empresa. Isso também fortalece a confiança dos clientes na qualidade do produto final.
5. Aumento da Segurança
Instrumentos com manutenção em dia ajudam a garantir condições mais seguras no ambiente de trabalho. Medições precisas são fundamentais para evitar riscos, principalmente em setores como a construção e a manufatura, onde erros podem resultar em acidentes. Uma medição adequada protege tanto os colaboradores quanto o negócio.
6. Eficiência Operacional
Instrumentos que funcionam de maneira eficiente contribuem para operações mais fluídas. Isso se traduz em um melhor desempenho através de processos mais rápidos e precisos, o que pode aumentar a produtividade geral da equipe e melhorar o tempo de resposta às demandas do mercado.
7. Melhoria na Qualidade do Produto
A qualidade final do produto é diretamente influenciada pela precisão das medições. A manutenção regular assegura que os instrumentos mantenham suas especificações, resultando em menos defeitos e maior satisfação do cliente. Isso pode ser um diferencial competitivo no mercado.
8. Feedback e Aprendizado Contínuo
Durante as inspeções de manutenção, os técnicos podem identificar possíveis áreas de melhoria nos processos de medição. Esse feedback é valioso para aprimorar técnicas de operação e aumentar a eficiência pode beneficiar tanto a manutenção dos instrumentos quanto a qualidade do trabalho realizado.
Em resumo, a manutenção regular de instrumentos de medição não é apenas uma prática recomendada, mas uma estratégia crítica que proporciona uma vasta gama de benefícios. Ao garantir a precisão, reduzir custos e melhorar a segurança, as empresas podem se posicionar de maneira mais forte no mercado e oferecer produtos de alta qualidade.
A calibração e manutenção de instrumentos de medição são fundamentais para assegurar a precisão e a confiabilidade nas medições realizadas em diversos setores.
Com a implementação de práticas regulares de calibração, as empresas não apenas atendem às normas regulamentares, mas também garantem a qualidade de seus produtos e serviços.
Identificar sinais de necessidade de manutenção, entender a frequência apropriada e seguir procedimentos de calibração adequados são passos cruciais para maximizar a vida útil e a eficiência dos instrumentos.
Através da manutenção continuamente praticada, é possível reduzir custos operacionais, aumentar a segurança no ambiente de trabalho e promover uma cultura de qualidade que beneficia a todos.
Portanto, investir no cuidado adequado dos instrumentos de medição é um passo estratégico para o sucesso a longo prazo de qualquer operação.