Calibração de Válvula de Segurança é Essencial para a Segurança Industrial
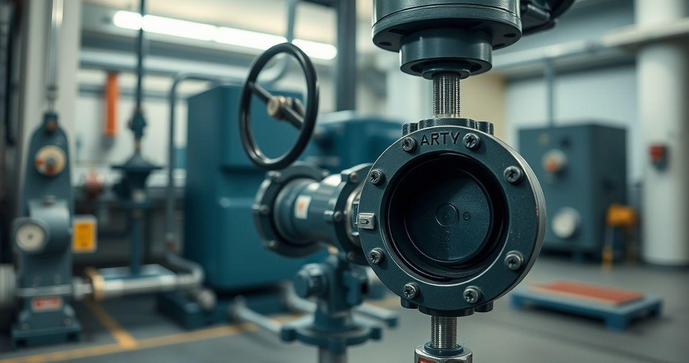
Por: Cláudio - 15 de Março de 2025
A calibração de válvula de segurança é um procedimento essencial para garantir a segurança e a eficiência em sistemas industriais. Essas válvulas desempenham um papel crucial na proteção de equipamentos e na prevenção de acidentes, controlando a pressão em sistemas pressurizados. Neste artigo, abordaremos a importância da calibração, os passos necessários para realizá-la corretamente, os erros comuns a serem evitados e a importância da manutenção regular para assegurar o funcionamento adequado das válvulas de segurança.
Importância da Calibração de Válvula de Segurança na Indústria
A calibração de válvula de segurança é um aspecto fundamental na operação de sistemas industriais, especialmente aqueles que lidam com fluidos pressurizados. Essas válvulas são projetadas para liberar pressão excessiva, evitando assim possíveis explosões ou falhas catastróficas. A calibração adequada garante que as válvulas funcionem dentro dos parâmetros especificados, proporcionando segurança e eficiência operacional.
Um dos principais motivos para a calibração de válvulas de segurança é a proteção de equipamentos e instalações. Em indústrias químicas, petroquímicas e de gás, por exemplo, a pressão excessiva pode levar a acidentes graves, resultando em danos materiais significativos e riscos à vida dos trabalhadores. A calibração regular assegura que as válvulas respondam corretamente a variações de pressão, evitando situações perigosas.
Além da segurança, a calibração de válvula de segurança também impacta a eficiência operacional. Válvulas mal calibradas podem levar a perdas de produto, desperdício de energia e aumento de custos operacionais. Quando uma válvula não abre na pressão correta, pode ocorrer um alívio inadequado, resultando em vazamentos ou falhas no sistema. Isso não apenas compromete a segurança, mas também afeta a produtividade da operação.
Outro ponto importante a ser considerado é a conformidade com normas e regulamentos. Muitas indústrias são obrigadas a seguir diretrizes rigorosas de segurança e qualidade, que incluem a calibração regular de válvulas de segurança. A não conformidade pode resultar em penalidades financeiras, interrupções na produção e danos à reputação da empresa. Portanto, manter um programa de calibração eficaz é essencial para garantir que a empresa esteja em conformidade com as regulamentações aplicáveis.
A calibração de válvula de segurança também desempenha um papel crucial na manutenção preditiva. Ao monitorar o desempenho das válvulas e realizar calibrações regulares, as empresas podem identificar problemas antes que se tornem críticos. Isso permite que as equipes de manutenção realizem intervenções planejadas, evitando paradas inesperadas e custos elevados de reparo. A manutenção preditiva, quando combinada com a calibração, resulta em um sistema mais confiável e eficiente.
Além disso, a calibração de válvula de segurança contribui para a longevidade do equipamento. Válvulas que são calibradas e mantidas adequadamente tendem a ter uma vida útil mais longa. Isso se traduz em menos substituições e, consequentemente, em uma redução nos custos operacionais. Investir na calibração regular é, portanto, uma estratégia inteligente para maximizar o retorno sobre o investimento em equipamentos.
É importante ressaltar que a calibração deve ser realizada por profissionais qualificados e com experiência. A complexidade dos sistemas industriais exige conhecimento técnico para garantir que as válvulas sejam calibradas corretamente. Além disso, o uso de equipamentos de calibração adequados é fundamental para obter resultados precisos. Empresas que oferecem serviços de calibração, como a Calibração de balanças, podem fornecer a expertise necessária para garantir que as válvulas de segurança estejam sempre em conformidade com os padrões exigidos.
Por fim, a calibração de válvula de segurança não deve ser vista apenas como uma obrigação, mas como uma prática essencial para a operação segura e eficiente de qualquer instalação industrial. A implementação de um programa de calibração robusto não apenas protege os trabalhadores e o ambiente, mas também melhora a eficiência e a rentabilidade da operação. Portanto, as empresas devem priorizar a calibração de suas válvulas de segurança como parte de sua estratégia de gestão de riscos e manutenção.
Em resumo, a calibração de válvula de segurança é vital para garantir a segurança, eficiência e conformidade nas operações industriais. Com a calibração adequada, as empresas podem minimizar riscos, reduzir custos e prolongar a vida útil de seus equipamentos. Investir na calibração regular é um passo crucial para qualquer organização que busca operar de maneira segura e eficiente.
Passos para Realizar a Calibração de Válvula de Segurança
A calibração de válvula de segurança é um processo crítico que deve ser realizado com precisão para garantir a segurança e a eficiência dos sistemas industriais. A seguir, apresentamos um guia passo a passo para realizar a calibração de válvulas de segurança, assegurando que elas funcionem corretamente e dentro dos parâmetros especificados.
1. Preparação e Planejamento
Antes de iniciar o processo de calibração, é fundamental realizar um planejamento adequado. Isso inclui a identificação da válvula a ser calibrada, a coleta de informações sobre suas especificações técnicas e a definição dos instrumentos de calibração necessários. É importante ter em mãos o manual do fabricante, que pode fornecer dados cruciais sobre a pressão de abertura e fechamento da válvula.
Além disso, é essencial garantir que a área de trabalho esteja limpa e organizada. Remova qualquer obstrução que possa interferir no processo de calibração e verifique se todos os equipamentos de segurança estão disponíveis e em boas condições. A segurança deve ser sempre a prioridade durante a calibração.
2. Desconexão da Válvula
O próximo passo é desconectar a válvula de segurança do sistema. Isso deve ser feito com cuidado para evitar danos à válvula ou ao sistema. Certifique-se de que não há pressão no sistema antes de desconectar a válvula. Utilize equipamentos de proteção individual (EPIs) adequados, como luvas e óculos de segurança, para garantir a segurança durante essa etapa.
3. Inspeção Visual
Antes de iniciar a calibração, é importante realizar uma inspeção visual da válvula. Verifique se há sinais de desgaste, corrosão ou danos. Componentes danificados podem afetar o desempenho da válvula e devem ser substituídos antes da calibração. A inspeção visual é uma etapa crucial que pode prevenir problemas futuros e garantir que a válvula funcione corretamente.
4. Configuração do Equipamento de Calibração
Após a inspeção, o próximo passo é configurar o equipamento de calibração. Isso pode incluir manômetros, bombas de pressão e outros dispositivos necessários para medir a pressão de abertura e fechamento da válvula. Certifique-se de que todos os instrumentos estejam calibrados e funcionando corretamente. A Calibração de torquímetro é um exemplo de serviço que pode ser necessário para garantir que os instrumentos de medição estejam precisos.
5. Realização da Calibração
Com o equipamento configurado, é hora de realizar a calibração. Aplique pressão gradualmente à válvula e monitore a pressão de abertura. A válvula deve abrir na pressão especificada pelo fabricante. Se a válvula abrir antes ou depois da pressão correta, ajustes devem ser feitos. Isso pode envolver a regulagem de molas ou outros componentes internos da válvula.
Após a abertura, continue a aumentar a pressão até que a válvula feche novamente. Registre a pressão de fechamento e compare com as especificações do fabricante. É importante que a válvula funcione corretamente em ambas as direções, abrindo e fechando nas pressões corretas.
6. Documentação dos Resultados
Após a calibração, todos os resultados devem ser documentados. Isso inclui as pressões de abertura e fechamento, bem como quaisquer ajustes realizados durante o processo. A documentação é essencial para garantir a conformidade com as normas e regulamentos, além de servir como referência para futuras calibrações.
7. Reinstalação da Válvula
Com a calibração concluída e os resultados documentados, a válvula pode ser reinstalada no sistema. Certifique-se de que todas as conexões estejam firmes e que não haja vazamentos. Após a reinstalação, é recomendável realizar um teste final para garantir que a válvula funcione corretamente dentro do sistema.
8. Manutenção e Verificação Regular
A calibração de válvula de segurança não deve ser um evento isolado. É importante estabelecer um cronograma de manutenção e verificação regular para garantir que as válvulas permaneçam em conformidade e funcionem corretamente ao longo do tempo. A manutenção preventiva pode ajudar a identificar problemas antes que se tornem críticos, garantindo a segurança e a eficiência do sistema.
Em resumo, a calibração de válvula de segurança é um processo que requer atenção aos detalhes e um planejamento cuidadoso. Seguir esses passos garantirá que as válvulas funcionem corretamente, proporcionando segurança e eficiência nas operações industriais. A calibração regular e a manutenção adequada são essenciais para maximizar a vida útil das válvulas e minimizar riscos operacionais.
Erros Comuns na Calibração de Válvula de Segurança
A calibração de válvula de segurança é um processo crítico que garante a segurança e a eficiência em sistemas industriais. No entanto, existem diversos erros que podem ocorrer durante esse procedimento, comprometendo a eficácia das válvulas e colocando em risco a segurança dos trabalhadores e das instalações. A seguir, discutiremos os erros mais comuns na calibração de válvula de segurança e como evitá-los.
1. Falta de Planejamento Adequado
Um dos erros mais frequentes na calibração de válvula de segurança é a falta de planejamento. Muitas vezes, as equipes de manutenção iniciam o processo sem uma compreensão clara das especificações da válvula ou dos requisitos de calibração. Isso pode levar a medições imprecisas e a ajustes inadequados. Para evitar esse erro, é fundamental revisar o manual do fabricante e coletar todas as informações necessárias antes de iniciar a calibração. Um planejamento adequado garante que todos os instrumentos e equipamentos necessários estejam disponíveis e prontos para uso.
2. Ignorar a Inspeção Visual
A inspeção visual da válvula antes da calibração é uma etapa crucial que não deve ser negligenciada. Ignorar essa etapa pode resultar em problemas não detectados, como desgaste, corrosão ou danos que podem afetar o desempenho da válvula. É importante realizar uma inspeção minuciosa para identificar quaisquer problemas que possam interferir na calibração. Se a válvula estiver danificada, ela deve ser reparada ou substituída antes de prosseguir com a calibração.
3. Uso de Equipamentos de Calibração Não Confiáveis
Outro erro comum é o uso de equipamentos de calibração que não estão devidamente calibrados ou que não são confiáveis. Instrumentos de medição imprecisos podem levar a resultados errôneos, comprometendo a calibração da válvula. É essencial garantir que todos os equipamentos de calibração estejam em boas condições e calibrados de acordo com os padrões apropriados. A Calibração de válvula de segurança deve ser realizada com instrumentos que garantam precisão e confiabilidade.
4. Não Realizar Ajustes Necessários
Durante o processo de calibração, é comum que as válvulas não abram ou fechem nas pressões especificadas. Um erro frequente é não realizar os ajustes necessários após a medição. Se a válvula não estiver funcionando corretamente, os técnicos devem ajustar os componentes internos, como molas ou mecanismos de acionamento, para garantir que a válvula opere nas pressões corretas. Ignorar essa etapa pode resultar em válvulas que não funcionam adequadamente, aumentando o risco de falhas no sistema.
5. Documentação Inadequada
A documentação dos resultados da calibração é uma parte essencial do processo, mas muitas vezes é negligenciada. A falta de registros precisos pode dificultar a identificação de problemas futuros e comprometer a conformidade com as normas e regulamentos. É importante documentar todas as medições, ajustes realizados e quaisquer observações relevantes durante a calibração. Essa documentação serve como referência para futuras calibrações e pode ser crucial em auditorias e inspeções.
6. Não Realizar Testes Finais
Após a calibração, é fundamental realizar testes finais para garantir que a válvula esteja funcionando corretamente dentro do sistema. Um erro comum é não realizar esses testes, o que pode resultar em válvulas que não operam como esperado. Os testes finais devem incluir a verificação da pressão de abertura e fechamento, bem como a observação do funcionamento da válvula em condições reais de operação. Essa etapa é crucial para garantir a segurança e a eficiência do sistema.
7. Ignorar a Manutenção Preventiva
A calibração de válvula de segurança não deve ser vista como um evento isolado. Ignorar a necessidade de manutenção preventiva pode levar a problemas recorrentes e à degradação do desempenho da válvula ao longo do tempo. É importante estabelecer um cronograma de manutenção regular que inclua calibrações periódicas e inspeções visuais. A manutenção preventiva ajuda a identificar problemas antes que se tornem críticos, garantindo a segurança e a eficiência do sistema.
8. Falta de Treinamento Adequado
Por fim, a falta de treinamento adequado para a equipe responsável pela calibração é um erro que pode ter consequências graves. Técnicos não treinados podem cometer erros durante o processo de calibração, resultando em medições imprecisas e ajustes inadequados. É fundamental que a equipe receba treinamento adequado sobre os procedimentos de calibração, o funcionamento das válvulas e o uso dos equipamentos de medição. Investir em treinamento garante que a calibração seja realizada de forma correta e segura.
Em resumo, a calibração de válvula de segurança é um processo que requer atenção aos detalhes e um entendimento claro dos procedimentos. Evitar os erros comuns mencionados acima é essencial para garantir que as válvulas funcionem corretamente e que a segurança do sistema seja mantida. Com um planejamento adequado, inspeções visuais, uso de equipamentos confiáveis e documentação precisa, as empresas podem minimizar riscos e garantir a eficiência de suas operações industriais.
Manutenção e Verificação Regular das Válvulas de Segurança
A manutenção e verificação regular das válvulas de segurança são essenciais para garantir a segurança e a eficiência em sistemas industriais. Essas válvulas desempenham um papel crucial na proteção de equipamentos e na prevenção de acidentes, controlando a pressão em sistemas pressurizados. A seguir, discutiremos a importância da manutenção regular, as melhores práticas e os benefícios de um programa de verificação eficaz.
1. Importância da Manutenção Regular
A manutenção regular das válvulas de segurança é fundamental para assegurar que elas funcionem corretamente quando necessário. Com o tempo, as válvulas podem sofrer desgaste devido a fatores como corrosão, acúmulo de sujeira e variações de pressão. Se não forem mantidas adequadamente, as válvulas podem falhar em abrir ou fechar nas pressões corretas, resultando em riscos significativos para a segurança dos trabalhadores e das instalações.
Além disso, a manutenção regular ajuda a identificar problemas antes que se tornem críticos. A detecção precoce de falhas pode evitar paradas inesperadas e custos elevados de reparo. Portanto, implementar um programa de manutenção preventiva é uma estratégia inteligente para maximizar a confiabilidade e a eficiência do sistema.
2. Frequência da Manutenção
A frequência da manutenção das válvulas de segurança pode variar dependendo de vários fatores, incluindo o tipo de válvula, as condições de operação e as recomendações do fabricante. Em geral, é aconselhável realizar inspeções visuais e testes de funcionamento pelo menos uma vez por ano. No entanto, em ambientes industriais mais exigentes, pode ser necessário aumentar a frequência das verificações.
Além das inspeções regulares, as válvulas devem ser recalibradas conforme necessário. A calibração deve ser realizada por profissionais qualificados, garantindo que as válvulas estejam sempre em conformidade com os padrões de segurança. Para isso, contar com uma Empresa de calibração de instrumentos de medição pode ser uma excelente opção para garantir a precisão e a confiabilidade dos equipamentos.
3. Procedimentos de Manutenção
Os procedimentos de manutenção das válvulas de segurança devem incluir uma série de etapas, começando pela inspeção visual. Durante essa inspeção, os técnicos devem verificar se há sinais de desgaste, corrosão ou danos. Componentes danificados devem ser substituídos imediatamente para evitar falhas no sistema.
Após a inspeção visual, é importante realizar testes de funcionamento. Isso envolve aplicar pressão à válvula e monitorar sua resposta. A válvula deve abrir e fechar nas pressões especificadas pelo fabricante. Se a válvula não funcionar corretamente, ajustes devem ser feitos para garantir que ela opere dentro dos parâmetros adequados.
Além disso, a limpeza das válvulas é uma parte essencial da manutenção. O acúmulo de sujeira e detritos pode interferir no funcionamento da válvula, levando a falhas. Portanto, é importante limpar regularmente as válvulas e seus componentes, garantindo que estejam livres de obstruções.
4. Documentação e Registro
A documentação adequada é uma parte crucial do processo de manutenção. Todos os resultados das inspeções, testes e ajustes devem ser registrados. Isso não apenas ajuda a manter um histórico da manutenção realizada, mas também é essencial para garantir a conformidade com as normas e regulamentos de segurança.
Além disso, a documentação pode ser útil para identificar padrões de falhas e determinar se há necessidade de melhorias no sistema. Manter registros precisos permite que as equipes de manutenção tomem decisões informadas sobre a necessidade de substituições ou atualizações de equipamentos.
5. Treinamento da Equipe
Um aspecto muitas vezes negligenciado na manutenção de válvulas de segurança é o treinamento da equipe responsável. Técnicos não treinados podem cometer erros durante a manutenção, resultando em medições imprecisas e ajustes inadequados. Portanto, é fundamental que a equipe receba treinamento adequado sobre os procedimentos de manutenção, o funcionamento das válvulas e o uso dos equipamentos de medição.
Investir em treinamento garante que a manutenção seja realizada de forma correta e segura, minimizando riscos e aumentando a eficiência do sistema. Além disso, a equipe deve estar atualizada sobre as melhores práticas e as novas tecnologias disponíveis no mercado.
6. Benefícios da Manutenção Regular
A manutenção e verificação regular das válvulas de segurança trazem uma série de benefícios para as operações industriais. Em primeiro lugar, garantem a segurança dos trabalhadores e das instalações, reduzindo o risco de acidentes e falhas catastróficas. Além disso, a manutenção regular contribui para a eficiência operacional, minimizando paradas inesperadas e custos elevados de reparo.
Outro benefício importante é a prolongação da vida útil das válvulas. Válvulas que são mantidas adequadamente tendem a ter uma vida útil mais longa, resultando em menos substituições e, consequentemente, em uma redução nos custos operacionais. A manutenção regular é, portanto, um investimento inteligente para maximizar o retorno sobre o investimento em equipamentos.
Em resumo, a manutenção e verificação regular das válvulas de segurança são essenciais para garantir a segurança, eficiência e confiabilidade em sistemas industriais. Implementar um programa de manutenção robusto, realizar inspeções regulares, documentar resultados e treinar a equipe são passos cruciais para maximizar a eficácia das válvulas de segurança e minimizar riscos operacionais. Ao priorizar a manutenção, as empresas podem operar de maneira mais segura e eficiente, protegendo seus trabalhadores e ativos.
Em conclusão, a calibração de válvula de segurança é um aspecto vital para a operação segura e eficiente de sistemas industriais. Através de um processo bem planejado e executado, é possível garantir que essas válvulas funcionem corretamente, protegendo equipamentos e prevenindo acidentes. A manutenção regular e a verificação das válvulas são igualmente importantes, pois ajudam a identificar problemas antes que se tornem críticos, assegurando a confiabilidade do sistema. Ao seguir as melhores práticas e evitar erros comuns, as empresas podem maximizar a segurança e a eficiência de suas operações, contribuindo para um ambiente de trabalho mais seguro e produtivo.