Calibração de Válvula de Segurança: Como Garantir a Eficiência e Segurança do Seu Sistema
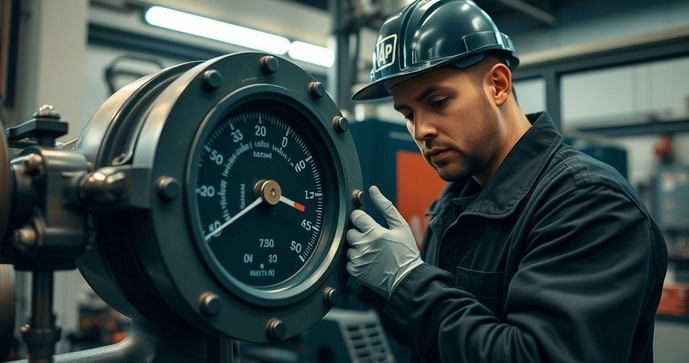
Por: Cláudio - 17 de Abril de 2025
A calibração de válvula de segurança é um processo crucial para garantir a eficiência e a segurança em sistemas industriais. Essas válvulas desempenham um papel vital na proteção de equipamentos e na prevenção de acidentes, controlando a pressão e evitando sobrecargas. Neste artigo, abordaremos a importância da calibração, o passo a passo para realizá-la corretamente, os erros comuns a serem evitados e a necessidade de manutenção regular para assegurar o funcionamento adequado das válvulas de segurança.
Importância da Calibração de Válvula de Segurança em Sistemas Industriais
A calibração de válvula de segurança é um aspecto fundamental na operação de sistemas industriais, especialmente em setores que lidam com substâncias perigosas ou que operam sob alta pressão. Essas válvulas são projetadas para proteger equipamentos e instalações, evitando acidentes que podem resultar em danos materiais, lesões e até fatalidades. A seguir, discutiremos a importância da calibração dessas válvulas e como ela contribui para a segurança e eficiência operacional.
Primeiramente, é essencial entender o papel das válvulas de segurança. Elas são dispositivos que atuam como uma linha de defesa contra a pressão excessiva em sistemas de tubulação e equipamentos. Quando a pressão interna atinge um nível crítico, a válvula se abre automaticamente, permitindo a liberação de fluidos ou gases, e assim prevenindo explosões ou falhas catastróficas. Portanto, a calibração adequada dessas válvulas é vital para garantir que elas funcionem corretamente quando necessário.
Um dos principais motivos para a calibração regular das válvulas de segurança é a manutenção da conformidade com normas e regulamentos de segurança. Muitas indústrias são obrigadas a seguir diretrizes rigorosas estabelecidas por órgãos reguladores, como a NR-13 no Brasil, que trata da segurança em caldeiras e vasos de pressão. A calibração garante que as válvulas atendam a esses padrões, evitando penalidades e garantindo a segurança dos trabalhadores e do ambiente.
Além disso, a calibração de válvula de segurança contribui para a eficiência operacional. Válvulas mal calibradas podem abrir em pressões inadequadas, resultando em perdas de produto e aumento de custos operacionais. Por exemplo, se uma válvula de segurança abrir muito cedo, pode causar a liberação desnecessária de vapor ou gás, levando a desperdícios e interrupções na produção. Por outro lado, se a válvula não abrir quando deveria, o risco de sobrepressão aumenta, colocando em perigo a integridade do sistema. Portanto, a calibração correta é essencial para otimizar o desempenho e minimizar custos.
Outro aspecto importante é a proteção do equipamento. Sistemas industriais frequentemente envolvem maquinário caro e complexo. A falha de uma válvula de segurança pode resultar em danos significativos a esses equipamentos, levando a paradas não programadas e custos de reparo elevados. A calibração regular ajuda a garantir que as válvulas estejam sempre prontas para atuar, protegendo assim o investimento da empresa e prolongando a vida útil dos equipamentos.
Além da proteção do equipamento, a calibração de válvula de segurança também é crucial para a segurança dos trabalhadores. Acidentes industriais podem ter consequências devastadoras, e a falha de uma válvula de segurança pode ser um fator determinante em muitos desses incidentes. A calibração adequada minimiza o risco de falhas, garantindo que as válvulas funcionem conforme o esperado em situações críticas. Isso não apenas protege os trabalhadores, mas também ajuda a criar um ambiente de trabalho mais seguro e confiável.
Ademais, a calibração de válvula de segurança deve ser realizada por profissionais qualificados, que compreendam as especificações técnicas e os requisitos de cada sistema. Esses especialistas são capazes de identificar problemas potenciais e realizar ajustes necessários, garantindo que as válvulas operem dentro dos parâmetros estabelecidos. A falta de conhecimento técnico pode levar a erros de calibração, comprometendo a segurança e a eficiência do sistema.
Por fim, é importante ressaltar que a calibração de válvula de segurança deve ser parte de um programa de manutenção preventiva mais amplo. Isso inclui a verificação regular de outros componentes do sistema, como medidores de pressão e dispositivos de controle. A integração de diferentes práticas de manutenção, como a calibração de balanças, pode ajudar a garantir que todos os aspectos do sistema estejam funcionando corretamente e em harmonia.
Em resumo, a calibração de válvula de segurança é um elemento crítico na operação de sistemas industriais. Ela não apenas garante a conformidade com normas de segurança, mas também otimiza a eficiência operacional, protege equipamentos e, acima de tudo, assegura a segurança dos trabalhadores. Investir em calibração regular e em profissionais qualificados é uma decisão inteligente que pode prevenir acidentes e economizar custos a longo prazo.
Passo a Passo para Realizar a Calibração de Válvula de Segurança
A calibração de válvula de segurança é um procedimento essencial para garantir que esses dispositivos funcionem corretamente e protejam sistemas industriais contra sobrepressão. A seguir, apresentamos um guia passo a passo para realizar a calibração de válvulas de segurança, assegurando que elas operem dentro dos parâmetros especificados pelo fabricante e pelas normas de segurança.
1. Preparação e Planejamento
Antes de iniciar o processo de calibração, é fundamental realizar um planejamento adequado. Isso inclui a coleta de informações sobre a válvula de segurança a ser calibrada, como seu modelo, especificações técnicas e requisitos de pressão. Além disso, é importante verificar se todos os equipamentos e ferramentas necessários estão disponíveis, como manômetros, chaves de fenda, e, se necessário, um calibração de torquímetro para garantir que as conexões estejam firmes e seguras.
2. Desligamento do Sistema
Antes de realizar qualquer trabalho na válvula de segurança, é crucial desligar o sistema em que ela está instalada. Isso garante a segurança do operador e evita acidentes. Certifique-se de que não há pressão no sistema e que a válvula esteja completamente despressurizada. É recomendável seguir os procedimentos de desligamento estabelecidos pela empresa e sinalizar a área para evitar que outros trabalhadores se aproximem durante a calibração.
3. Remoção da Válvula de Segurança
Após garantir que o sistema está desligado e despressurizado, o próximo passo é remover a válvula de segurança. Utilize as ferramentas adequadas para soltar a válvula do sistema, tomando cuidado para não danificar as conexões ou os componentes adjacentes. Armazene a válvula em um local seguro e limpo, onde não corra o risco de contaminação ou danos.
4. Inspeção Visual
Antes de iniciar a calibração, é importante realizar uma inspeção visual da válvula de segurança. Verifique se há sinais de desgaste, corrosão ou danos. Componentes danificados podem comprometer a eficácia da válvula e devem ser substituídos antes da calibração. Além disso, verifique se as superfícies de vedação estão limpas e livres de detritos, pois isso pode afetar o desempenho da válvula.
5. Conexão do Manômetro
Para calibrar a válvula de segurança, é necessário conectar um manômetro à entrada da válvula. O manômetro deve ser calibrado e adequado para a faixa de pressão que será testada. Certifique-se de que as conexões estão firmes e seguras para evitar vazamentos durante o teste. O manômetro permitirá monitorar a pressão enquanto a válvula é testada.
6. Teste de Pressão
Com a válvula de segurança conectada ao manômetro, inicie o teste de pressão. Gradualmente, aumente a pressão do sistema até atingir o ponto de abertura especificado para a válvula. Durante esse processo, observe o manômetro para garantir que a pressão esteja aumentando de forma controlada. Quando a válvula abrir, anote a pressão em que isso ocorreu. Essa pressão deve estar dentro dos limites especificados pelo fabricante.
7. Ajustes Necessários
Se a pressão de abertura da válvula não estiver dentro dos parâmetros especificados, será necessário realizar ajustes. A maioria das válvulas de segurança possui um mecanismo de ajuste que permite alterar a pressão de abertura. Siga as instruções do fabricante para realizar os ajustes adequados. Após fazer as alterações, repita o teste de pressão para verificar se a válvula agora abre na pressão correta.
8. Teste de Fechamento
Após calibrar a pressão de abertura, é importante realizar um teste de fechamento. Para isso, reduza a pressão do sistema até que a válvula se feche completamente. O fechamento deve ocorrer em uma pressão que não cause sobrepressão no sistema. Anote a pressão em que a válvula se fecha, pois isso também deve estar dentro dos parâmetros especificados.
9. Documentação
Após concluir a calibração, é fundamental documentar todos os resultados dos testes, incluindo as pressões de abertura e fechamento, bem como quaisquer ajustes realizados. Essa documentação é importante para garantir a conformidade com as normas de segurança e para futuras referências. Além disso, pode ser útil para auditorias e inspeções.
10. Reinstalação da Válvula
Com a calibração concluída e a documentação em mãos, a próxima etapa é reinstalar a válvula de segurança no sistema. Certifique-se de que todas as conexões estejam firmes e seguras. Após a instalação, é recomendável realizar um teste final no sistema para garantir que a válvula funcione corretamente em condições operacionais.
11. Manutenção Regular
A calibração de válvula de segurança não deve ser um evento isolado. É importante estabelecer um cronograma de manutenção regular para garantir que as válvulas permaneçam em boas condições de funcionamento. Isso inclui inspeções visuais periódicas, testes de pressão e ajustes conforme necessário. A manutenção preventiva ajuda a evitar falhas e a garantir a segurança do sistema.
Em resumo, a calibração de válvula de segurança é um processo crítico que envolve várias etapas, desde a preparação até a documentação dos resultados. Seguir este passo a passo garante que as válvulas operem de forma eficaz e segura, protegendo tanto os equipamentos quanto os trabalhadores. A realização de calibrações regulares e a manutenção adequada são essenciais para a segurança e eficiência dos sistemas industriais.
Erros Comuns na Calibração de Válvula de Segurança e Como Evitá-los
A calibração de válvula de segurança é um procedimento crítico para garantir a segurança e a eficiência de sistemas industriais. No entanto, existem diversos erros que podem ocorrer durante esse processo, comprometendo a eficácia da válvula e colocando em risco a segurança do ambiente de trabalho. A seguir, discutiremos os erros mais comuns na calibração de válvula de segurança e como evitá-los.
1. Falta de Planejamento Adequado
Um dos erros mais frequentes é a falta de planejamento antes de iniciar a calibração. Muitas vezes, os profissionais começam o processo sem ter todas as informações necessárias sobre a válvula, como especificações técnicas e requisitos de pressão. Para evitar esse erro, é fundamental realizar uma pesquisa prévia e reunir todos os dados relevantes. Isso inclui entender o modelo da válvula, as pressões de abertura e fechamento recomendadas e as ferramentas necessárias para a calibração.
2. Ignorar as Instruções do Fabricante
Outro erro comum é desconsiderar as instruções do fabricante durante a calibração. Cada válvula de segurança possui características específicas e requer procedimentos de calibração distintos. Ignorar essas diretrizes pode resultar em calibrações incorretas e falhas no funcionamento da válvula. Para evitar esse problema, sempre consulte o manual do fabricante e siga as orientações fornecidas. Isso garantirá que a calibração seja realizada de acordo com os padrões estabelecidos.
3. Não Realizar Inspeções Visuais
A calibração de válvula de segurança deve ser precedida por uma inspeção visual cuidadosa. Muitos profissionais pulam essa etapa, o que pode levar a problemas sérios. Componentes danificados ou desgastados podem comprometer a eficácia da válvula e causar falhas durante a operação. Para evitar esse erro, sempre faça uma inspeção minuciosa antes de iniciar a calibração. Verifique se há sinais de corrosão, desgaste ou danos e substitua qualquer componente que não esteja em boas condições.
4. Conexões Inadequadas
As conexões entre a válvula de segurança e o manômetro devem ser firmes e seguras. Conexões inadequadas podem resultar em vazamentos e leituras imprecisas durante o teste de pressão. Para evitar esse erro, certifique-se de que todas as conexões estejam bem apertadas e que não haja folgas. Utilize ferramentas apropriadas para garantir que as conexões estejam firmes, evitando assim problemas durante a calibração.
5. Testes de Pressão Mal Conduzidos
Realizar testes de pressão de forma inadequada é um erro que pode comprometer a calibração da válvula de segurança. Isso inclui aumentar a pressão muito rapidamente ou não monitorar a pressão de forma adequada. Para evitar esse problema, aumente a pressão gradualmente e monitore o manômetro com atenção. Anote a pressão em que a válvula abre e fecha, garantindo que esses valores estejam dentro dos parâmetros especificados pelo fabricante.
6. Não Registrar os Resultados
A documentação é uma parte crucial do processo de calibração, mas muitos profissionais não registram os resultados dos testes. Isso pode levar a dificuldades em auditorias e inspeções futuras, além de dificultar a identificação de problemas recorrentes. Para evitar esse erro, sempre documente os resultados da calibração, incluindo as pressões de abertura e fechamento, ajustes realizados e quaisquer observações relevantes. Essa documentação é essencial para garantir a conformidade com as normas de segurança e para futuras referências.
7. Ignorar a Manutenção Regular
A calibração de válvula de segurança não deve ser um evento isolado. Ignorar a necessidade de manutenção regular é um erro que pode levar a falhas no sistema. As válvulas devem ser inspecionadas e calibradas periodicamente para garantir que continuem a operar de forma eficaz. Para evitar esse problema, estabeleça um cronograma de manutenção regular que inclua inspeções visuais, testes de pressão e calibrações conforme necessário. Isso ajudará a garantir que as válvulas permaneçam em boas condições de funcionamento.
8. Falta de Treinamento Adequado
Um erro comum na calibração de válvula de segurança é a falta de treinamento adequado dos profissionais responsáveis pelo processo. A calibração requer conhecimento técnico e habilidades específicas, e a falta de formação pode resultar em erros significativos. Para evitar esse problema, invista em treinamento para sua equipe. Isso garantirá que os profissionais estejam capacitados para realizar a calibração de forma correta e segura.
9. Não Considerar as Condições Ambientais
As condições ambientais podem afetar o desempenho das válvulas de segurança. Ignorar fatores como temperatura, umidade e presença de contaminantes pode levar a falhas na calibração. Para evitar esse erro, considere as condições ambientais ao realizar a calibração. Certifique-se de que a válvula esteja em um ambiente adequado e que não haja fatores externos que possam interferir no funcionamento da válvula.
10. Subestimar a Importância da Calibração
Por fim, um dos maiores erros é subestimar a importância da calibração de válvula de segurança. Muitas vezes, as empresas podem ver a calibração como uma tarefa secundária, mas isso pode ter consequências graves. A calibração inadequada pode resultar em falhas catastróficas, colocando em risco a segurança dos trabalhadores e a integridade do sistema. Para evitar esse erro, reconheça a calibração como uma parte essencial da manutenção de segurança e eficiência operacional.
Em resumo, a calibração de válvula de segurança é um processo crítico que deve ser realizado com atenção e cuidado. Evitar os erros comuns mencionados acima é fundamental para garantir que as válvulas operem de forma eficaz e segura. Investir em planejamento, seguir as instruções do fabricante, realizar inspeções visuais e documentar os resultados são práticas que ajudarão a garantir a segurança e a eficiência dos sistemas industriais. A calibração de válvula de segurança deve ser uma prioridade para todas as empresas que buscam manter um ambiente de trabalho seguro e eficiente.
Manutenção e Verificação Regular da Válvula de Segurança
A manutenção e verificação regular da válvula de segurança são essenciais para garantir a segurança e a eficiência de sistemas industriais. Essas válvulas desempenham um papel crucial na proteção de equipamentos e na prevenção de acidentes, controlando a pressão em sistemas de tubulação e evitando sobrecargas. Neste artigo, discutiremos a importância da manutenção regular, as práticas recomendadas e como garantir que as válvulas de segurança operem de forma eficaz ao longo do tempo.
1. Importância da Manutenção Regular
A manutenção regular das válvulas de segurança é fundamental para assegurar que elas funcionem corretamente quando necessário. Com o tempo, componentes mecânicos podem se desgastar, e a corrosão pode afetar a eficácia da válvula. A falta de manutenção pode levar a falhas catastróficas, resultando em acidentes, danos materiais e até mesmo ferimentos. Portanto, realizar verificações e manutenções periódicas é uma prática essencial para garantir a segurança dos trabalhadores e a integridade dos sistemas.
2. Frequência das Manutenções
A frequência das manutenções pode variar dependendo do tipo de sistema, das condições operacionais e das recomendações do fabricante. Em geral, é aconselhável realizar inspeções visuais e testes de funcionamento a cada seis meses. No entanto, sistemas que operam em condições extremas ou que lidam com substâncias corrosivas podem exigir manutenções mais frequentes. É importante seguir as diretrizes do fabricante e adaptar o cronograma de manutenção às necessidades específicas de cada sistema.
3. Inspeções Visuais
As inspeções visuais são uma parte crucial da manutenção regular. Durante essas inspeções, os profissionais devem verificar se há sinais de desgaste, corrosão ou danos na válvula e em seus componentes. É importante observar as superfícies de vedação, as conexões e os mecanismos de acionamento. Qualquer sinal de deterioração deve ser tratado imediatamente, substituindo peças danificadas ou realizando reparos conforme necessário. Além disso, a limpeza das válvulas e das áreas ao redor é fundamental para evitar a acumulação de sujeira e detritos que possam interferir no funcionamento.
4. Testes de Funcionamento
Além das inspeções visuais, é essencial realizar testes de funcionamento regulares. Esses testes garantem que a válvula de segurança abra e feche nas pressões corretas. Para isso, é necessário conectar um manômetro à válvula e aumentar a pressão gradualmente até atingir o ponto de abertura. O teste deve ser realizado em condições controladas, e os resultados devem ser registrados para garantir a conformidade com as especificações do fabricante. Caso a válvula não funcione corretamente, ajustes ou substituições devem ser realizados imediatamente.
5. Documentação e Registro
Manter registros detalhados das manutenções e verificações realizadas é uma prática recomendada que não deve ser negligenciada. A documentação deve incluir informações sobre as inspeções visuais, testes de funcionamento, ajustes realizados e quaisquer peças substituídas. Esses registros são importantes para auditorias e inspeções futuras, além de ajudar a identificar padrões de desgaste e a necessidade de manutenções adicionais. A documentação adequada também demonstra o compromisso da empresa com a segurança e a conformidade regulatória.
6. Treinamento da Equipe
Um aspecto frequentemente esquecido na manutenção de válvulas de segurança é a importância do treinamento da equipe responsável. Profissionais bem treinados são mais propensos a identificar problemas potenciais e a realizar manutenções de forma eficaz. Investir em treinamento contínuo para a equipe garante que todos estejam atualizados sobre as melhores práticas e as últimas tecnologias. Isso não apenas melhora a segurança, mas também aumenta a eficiência operacional.
7. Consultoria Especializada
Em alguns casos, pode ser benéfico contar com a ajuda de uma empresa de calibração de instrumentos de medição especializada. Esses profissionais têm o conhecimento e a experiência necessários para realizar calibrações e manutenções de forma precisa e eficiente. Além disso, eles podem fornecer orientações sobre as melhores práticas e ajudar a identificar áreas que precisam de atenção especial. A consultoria especializada pode ser um investimento valioso para garantir a segurança e a eficiência do sistema.
8. Atualização de Equipamentos
À medida que a tecnologia avança, pode ser necessário atualizar as válvulas de segurança e outros componentes do sistema. Válvulas mais novas podem oferecer melhor desempenho, maior eficiência e recursos adicionais que melhoram a segurança. Avaliar periodicamente a necessidade de atualização é uma parte importante da manutenção. Isso garante que o sistema esteja sempre operando com a melhor tecnologia disponível, minimizando riscos e maximizando a eficiência.
9. Conclusão
A manutenção e verificação regular da válvula de segurança são essenciais para garantir a segurança e a eficiência de sistemas industriais. Realizar inspeções visuais, testes de funcionamento, manter documentação adequada e investir no treinamento da equipe são práticas fundamentais que ajudam a evitar falhas e a garantir a conformidade com as normas de segurança. Contar com a ajuda de uma empresa especializada em calibração de instrumentos de medição pode ser um diferencial importante para manter a segurança e a eficiência operacional. Ao priorizar a manutenção regular, as empresas podem proteger seus trabalhadores, seus equipamentos e seus investimentos, criando um ambiente de trabalho mais seguro e eficiente.
Em resumo, a calibração de válvula de segurança é um procedimento essencial que não deve ser negligenciado em ambientes industriais. Através da calibração adequada, é possível garantir que essas válvulas operem dentro dos parâmetros especificados, protegendo equipamentos e assegurando a segurança dos trabalhadores. Além disso, a manutenção regular e a verificação frequente são fundamentais para evitar falhas e prolongar a vida útil das válvulas. Ao seguir as melhores práticas e estar atento aos erros comuns, as empresas podem criar um ambiente de trabalho mais seguro e eficiente, minimizando riscos e maximizando a produtividade. Investir na calibração e manutenção das válvulas de segurança é, portanto, um passo crucial para qualquer operação industrial que valorize a segurança e a eficiência.