Calibração de Instrumentos de Medição: Garantindo Precisão e Confiabilidade em Seus Resultados
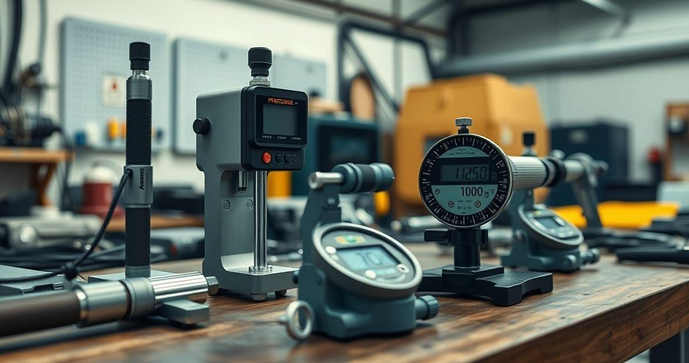
Por: Cláudio - 17 de Abril de 2025
A calibração de instrumentos de medição é um processo fundamental para garantir a precisão e a confiabilidade dos resultados obtidos em diversas aplicações. Seja na indústria, laboratórios ou em ambientes de pesquisa, a correta calibração assegura que os instrumentos estejam funcionando dentro dos padrões estabelecidos. Neste artigo, abordaremos a importância da calibração, os métodos utilizados, a frequência recomendada e os erros comuns que podem ocorrer durante o processo.
Importância da Calibração de Instrumentos de Medição
A calibração de instrumentos de medição é um procedimento essencial que garante a precisão e a confiabilidade dos dados obtidos em diversas áreas, como indústria, laboratórios, saúde e pesquisa científica. Através da calibração, é possível ajustar os instrumentos para que suas medições estejam em conformidade com padrões estabelecidos, assegurando que os resultados sejam válidos e utilizáveis. A seguir, discutiremos a importância da calibração de instrumentos de medição e como ela impacta diferentes setores.
Um dos principais motivos para realizar a calibração é a necessidade de garantir a precisão das medições. Instrumentos de medição, como balanças, termômetros e manômetros, podem sofrer desgastes ao longo do tempo, resultando em leituras imprecisas. Isso pode ocorrer devido a fatores como variações de temperatura, umidade, vibrações e até mesmo o uso inadequado. A calibração regular ajuda a identificar e corrigir esses desvios, assegurando que os instrumentos estejam sempre operando dentro das especificações desejadas.
Além da precisão, a calibração é crucial para a conformidade com normas e regulamentos. Muitas indústrias e laboratórios são obrigados a seguir padrões específicos, como os estabelecidos pela ISO (Organização Internacional de Normalização) e pela ANVISA (Agência Nacional de Vigilância Sanitária). A calibração de instrumentos de medição é uma exigência para garantir que os processos atendam a essas normas, evitando problemas legais e garantindo a qualidade dos produtos e serviços oferecidos. Por exemplo, a Calibração de balanças é um procedimento comum em setores que lidam com pesagens, como o alimentício e farmacêutico, onde a precisão é vital.
Outro aspecto importante da calibração é a segurança. Em setores como a saúde, onde instrumentos de medição são utilizados para diagnósticos e tratamentos, a precisão é fundamental para garantir a segurança dos pacientes. Um termômetro que não está calibrado corretamente pode levar a diagnósticos errôneos, resultando em tratamentos inadequados. A calibração regular desses instrumentos é, portanto, uma prática essencial para proteger a saúde e o bem-estar dos indivíduos.
Além disso, a calibração contribui para a eficiência operacional. Instrumentos de medição que não estão calibrados podem resultar em desperdício de materiais, tempo e recursos. Por exemplo, em uma linha de produção, uma balança que não está funcionando corretamente pode levar a erros na dosagem de ingredientes, resultando em produtos fora das especificações. Isso não apenas afeta a qualidade do produto final, mas também pode gerar custos adicionais com retrabalho e desperdício. A calibração regular ajuda a minimizar esses riscos, garantindo que os processos sejam realizados de forma eficiente e econômica.
A calibração também desempenha um papel importante na melhoria contínua dos processos. Ao monitorar e calibrar instrumentos de medição, as empresas podem identificar tendências e padrões que podem indicar a necessidade de ajustes nos processos. Isso permite que as organizações implementem melhorias e inovações, aumentando a competitividade no mercado. A calibração, portanto, não é apenas uma questão de conformidade, mas também uma oportunidade para otimizar operações e aumentar a qualidade dos produtos e serviços.
Por fim, a calibração de instrumentos de medição é uma prática que promove a confiança entre os stakeholders. Clientes, fornecedores e reguladores esperam que as medições sejam precisas e confiáveis. Ao investir em calibração, as empresas demonstram seu compromisso com a qualidade e a transparência, fortalecendo a confiança em suas operações. Isso é especialmente importante em setores onde a reputação e a credibilidade são fundamentais para o sucesso a longo prazo.
Em resumo, a calibração de instrumentos de medição é uma prática indispensável que impacta diretamente a precisão, a conformidade, a segurança, a eficiência operacional e a confiança nas operações. Através da calibração regular, as organizações podem garantir que seus instrumentos estejam sempre em conformidade com os padrões estabelecidos, promovendo a qualidade e a segurança em seus processos. Portanto, é essencial que empresas de todos os setores reconheçam a importância da calibração e implementem programas eficazes para garantir a precisão de suas medições.
Métodos Comuns de Calibração
A calibração de instrumentos de medição é um processo fundamental para garantir a precisão e a confiabilidade das medições em diversas aplicações. Existem vários métodos de calibração, cada um adequado a diferentes tipos de instrumentos e contextos. Neste artigo, abordaremos alguns dos métodos mais comuns de calibração, suas características e quando utilizá-los.
Um dos métodos mais tradicionais de calibração é a calibração por comparação. Este método envolve a comparação do instrumento a ser calibrado com um padrão de referência conhecido e rastreável. O padrão de referência deve ter uma precisão superior à do instrumento em teste. Durante o processo, o instrumento é submetido a medições em condições controladas, e os resultados são comparados com os valores do padrão. Essa abordagem é amplamente utilizada em laboratórios e indústrias, pois permite identificar desvios e ajustar o instrumento conforme necessário.
Outro método comum é a calibração por ajuste. Neste caso, o instrumento é ajustado diretamente para que suas medições correspondam aos valores de um padrão de referência. Esse método é frequentemente utilizado em instrumentos que possuem um mecanismo de ajuste interno, como balanças e termômetros. A calibração por ajuste é eficaz, pois não apenas identifica desvios, mas também corrige os problemas, garantindo que o instrumento funcione corretamente após o processo. Por exemplo, a Calibração de torquímetro é um procedimento que pode envolver ajustes diretos para garantir que o torque aplicado esteja dentro das especificações desejadas.
A calibração por transferência é outro método utilizado, especialmente em situações onde a calibração direta não é viável. Nesse caso, um instrumento de medição é calibrado em relação a outro instrumento que já foi calibrado e é considerado um padrão. Este método é útil em ambientes de produção, onde a calibração frequente de todos os instrumentos pode ser impraticável. A calibração por transferência permite que um instrumento calibrado seja utilizado como referência para calibrar outros instrumentos, mantendo a precisão e a confiabilidade das medições.
Além disso, a calibração em campo é um método que se tornou cada vez mais popular, especialmente em aplicações industriais. Esse método envolve a calibração de instrumentos diretamente no local onde eles são utilizados, em vez de enviá-los para um laboratório. A calibração em campo é vantajosa porque permite que os instrumentos sejam ajustados em suas condições reais de operação, levando em consideração fatores como temperatura, umidade e vibrações. Isso é particularmente importante para instrumentos que podem ser afetados por essas variáveis, garantindo que as medições sejam precisas e relevantes para o ambiente de trabalho.
Outro método importante é a calibração por simulação. Este método é utilizado principalmente em instrumentos que não podem ser calibrados diretamente devido a limitações técnicas. A calibração por simulação envolve a criação de condições de teste que imitam as condições reais de operação do instrumento. Por exemplo, em instrumentos de medição de pressão, pode-se simular diferentes pressões para verificar a resposta do instrumento. Esse método é útil para validar o desempenho de instrumentos em situações específicas, garantindo que eles funcionem corretamente em uma variedade de condições.
A calibração por meio de software também tem ganhado destaque, especialmente com o avanço da tecnologia. Muitos instrumentos modernos vêm equipados com software que permite a calibração automática ou semi-automática. Esses sistemas utilizam algoritmos para ajustar as medições com base em dados de referência, facilitando o processo de calibração e reduzindo a possibilidade de erro humano. A calibração por software é especialmente útil em ambientes de produção em larga escala, onde a eficiência e a precisão são cruciais.
Por fim, a calibração de múltiplos pontos é um método que envolve a calibração do instrumento em vários pontos de medição, em vez de apenas um. Esse método é importante para instrumentos que apresentam não linearidade em suas medições. Ao calibrar em múltiplos pontos, é possível criar uma curva de calibração que representa com precisão o desempenho do instrumento em toda a sua faixa de operação. Isso garante que as medições sejam precisas em todas as condições de uso.
Em resumo, existem diversos métodos de calibração que podem ser utilizados, dependendo do tipo de instrumento, das condições de operação e das necessidades específicas de cada aplicação. A escolha do método adequado é fundamental para garantir a precisão e a confiabilidade das medições. A calibração regular e eficaz não apenas assegura a conformidade com normas e regulamentos, mas também contribui para a eficiência operacional e a segurança em diversos setores. Portanto, é essencial que as organizações reconheçam a importância da calibração e implementem os métodos mais apropriados para seus instrumentos de medição.
Frequência Recomendada para Calibração
A calibração de instrumentos de medição é uma prática essencial para garantir a precisão e a confiabilidade das medições em diversos setores. No entanto, a eficácia da calibração não depende apenas da qualidade do processo, mas também da frequência com que ela é realizada. A determinação da frequência recomendada para calibração é um aspecto crítico que pode variar de acordo com o tipo de instrumento, a aplicação e as condições de uso. Neste artigo, discutiremos a importância da frequência de calibração, os fatores que influenciam essa decisão e as recomendações gerais para diferentes tipos de instrumentos.
Um dos principais fatores a considerar ao determinar a frequência de calibração é o tipo de instrumento. Instrumentos que são utilizados em ambientes críticos, como laboratórios de pesquisa ou indústrias farmacêuticas, geralmente exigem calibrações mais frequentes. Isso se deve à necessidade de garantir que as medições sejam sempre precisas e confiáveis, uma vez que pequenos desvios podem ter consequências significativas. Por exemplo, a Calibração de válvula de segurança é um procedimento que deve ser realizado regularmente para garantir que esses dispositivos funcionem corretamente e protejam os sistemas de pressão de falhas catastróficas.
Outro fator a ser considerado é a frequência de uso do instrumento. Instrumentos que são utilizados com alta frequência tendem a sofrer mais desgaste e, portanto, podem exigir calibrações mais frequentes. Por exemplo, uma balança utilizada diariamente em um ambiente de produção pode precisar ser calibrada mensalmente, enquanto uma balança que é usada apenas ocasionalmente pode ser calibrada a cada seis meses ou anualmente. A intensidade do uso está diretamente relacionada à precisão das medições, e a calibração regular ajuda a garantir que os instrumentos permaneçam dentro das especificações desejadas.
As condições ambientais também desempenham um papel importante na determinação da frequência de calibração. Instrumentos que operam em ambientes com variações extremas de temperatura, umidade ou vibrações podem exigir calibrações mais frequentes. Essas condições podem afetar o desempenho dos instrumentos e levar a desvios nas medições. Portanto, é fundamental considerar o ambiente em que o instrumento está sendo utilizado ao estabelecer um cronograma de calibração. Em ambientes industriais, onde as condições podem ser adversas, a calibração pode ser necessária a cada três meses, enquanto em ambientes controlados, a calibração pode ser realizada anualmente.
Além disso, a natureza da aplicação também influencia a frequência de calibração. Em setores onde a precisão é crítica, como na indústria alimentícia ou farmacêutica, a calibração deve ser realizada com mais frequência. Isso se deve ao fato de que erros nas medições podem resultar em produtos inseguros ou não conformes. Por outro lado, em aplicações menos críticas, a frequência de calibração pode ser estendida. É importante que as organizações avaliem as necessidades específicas de suas operações e ajustem a frequência de calibração de acordo.
As recomendações de calibração também podem ser influenciadas por normas e regulamentos específicos do setor. Muitas indústrias têm diretrizes estabelecidas que determinam a frequência mínima de calibração para diferentes tipos de instrumentos. Por exemplo, a ISO 9001, uma norma internacional de gestão da qualidade, recomenda que as organizações estabeleçam um cronograma de calibração baseado em critérios como a frequência de uso, as condições ambientais e a importância da precisão das medições. Seguir essas diretrizes ajuda a garantir a conformidade e a qualidade dos processos.
Além disso, a calibração deve ser realizada sempre que houver uma mudança significativa nas condições de operação. Isso pode incluir a mudança de um local de uso, a introdução de novos processos ou a realização de manutenção nos instrumentos. Essas alterações podem afetar a precisão das medições e, portanto, a calibração deve ser realizada para garantir que os instrumentos estejam funcionando corretamente após qualquer modificação.
Por fim, é importante que as organizações mantenham registros detalhados das calibrações realizadas, incluindo datas, resultados e quaisquer ajustes feitos. Esses registros são essenciais para monitorar a eficácia do programa de calibração e para identificar tendências que possam indicar a necessidade de ajustes na frequência de calibração. Além disso, esses registros podem ser úteis em auditorias e inspeções, demonstrando o compromisso da organização com a qualidade e a conformidade.
Em resumo, a frequência recomendada para calibração é um aspecto crítico que deve ser cuidadosamente considerado por organizações de todos os setores. Fatores como o tipo de instrumento, a frequência de uso, as condições ambientais e a natureza da aplicação desempenham um papel importante na determinação da frequência de calibração. Ao estabelecer um cronograma de calibração adequado, as organizações podem garantir a precisão e a confiabilidade de suas medições, promovendo a qualidade e a segurança em suas operações. A calibração regular não apenas ajuda a atender às normas e regulamentos, mas também contribui para a eficiência operacional e a confiança nas medições realizadas.
Erros Comuns na Calibração e Como Evitá-los
A calibração de instrumentos de medição é um processo crítico que garante a precisão e a confiabilidade das medições em diversas aplicações. No entanto, erros podem ocorrer durante esse processo, comprometendo a eficácia da calibração e, consequentemente, a qualidade dos resultados obtidos. Neste artigo, discutiremos alguns dos erros mais comuns na calibração e como evitá-los, garantindo que os instrumentos funcionem corretamente e atendam às especificações necessárias.
Um dos erros mais frequentes na calibração é a falta de um padrão de referência adequado. A calibração deve ser realizada em comparação com um padrão que tenha uma precisão superior ao instrumento em teste. Se o padrão de referência não for rastreável ou não atender aos requisitos de precisão, os resultados da calibração podem ser imprecisos. Para evitar esse erro, é fundamental utilizar padrões de referência que sejam calibrados e certificados por organismos competentes. Além disso, é importante garantir que esses padrões sejam mantidos em condições adequadas e que sua calibração seja verificada regularmente.
Outro erro comum é a calibração em condições inadequadas. A temperatura, umidade e vibrações podem afetar significativamente o desempenho dos instrumentos de medição. Realizar a calibração em um ambiente que não esteja controlado pode levar a resultados imprecisos. Para evitar esse problema, é essencial realizar a calibração em um ambiente controlado, onde as condições possam ser monitoradas e mantidas dentro dos limites especificados. Isso é especialmente importante em laboratórios e indústrias onde a precisão é crítica.
A falta de treinamento adequado dos profissionais responsáveis pela calibração também é um erro que pode comprometer a qualidade do processo. A calibração requer conhecimento técnico e habilidades específicas para garantir que os instrumentos sejam calibrados corretamente. Profissionais não treinados podem cometer erros durante a calibração, resultando em medições imprecisas. Para evitar esse problema, as organizações devem investir em treinamento contínuo para suas equipes, garantindo que todos os envolvidos no processo de calibração estejam atualizados sobre as melhores práticas e procedimentos.
Além disso, a falta de documentação adequada pode levar a erros na calibração. Registros incompletos ou ausentes podem dificultar a identificação de problemas e a verificação da conformidade com os padrões estabelecidos. É fundamental manter registros detalhados de todas as calibrações realizadas, incluindo datas, resultados, ajustes feitos e condições de operação. Esses registros não apenas ajudam a monitorar a eficácia do programa de calibração, mas também são essenciais para auditorias e inspeções. Para garantir a qualidade, considere trabalhar com uma Empresa de calibração de instrumentos de medição que possa fornecer suporte e documentação adequada.
Outro erro comum é a calibração em intervalos inadequados. A frequência de calibração deve ser determinada com base em fatores como o tipo de instrumento, a frequência de uso e as condições ambientais. Calibrar instrumentos com muita frequência pode resultar em custos desnecessários, enquanto calibrações raras podem levar a medições imprecisas. Para evitar esse erro, as organizações devem estabelecer um cronograma de calibração baseado em uma análise cuidadosa das necessidades específicas de seus instrumentos e operações. Isso pode incluir a realização de calibrações regulares, bem como a verificação da necessidade de calibrações adicionais após mudanças nas condições de operação.
A falta de verificação dos resultados da calibração também é um erro que pode comprometer a qualidade do processo. Após a calibração, é importante realizar testes de verificação para garantir que o instrumento esteja funcionando corretamente e que as medições estejam dentro das especificações. Ignorar essa etapa pode resultar em instrumentos que não estão calibrados corretamente, levando a medições imprecisas. Para evitar esse problema, as organizações devem implementar procedimentos de verificação após cada calibração, garantindo que os instrumentos estejam prontos para uso.
Além disso, a utilização de equipamentos inadequados ou danificados durante o processo de calibração pode levar a erros. Instrumentos que não estão em boas condições podem afetar a precisão das medições e comprometer os resultados da calibração. Para evitar esse erro, é fundamental realizar inspeções regulares nos equipamentos utilizados na calibração e garantir que estejam em boas condições de funcionamento. Isso inclui a verificação de cabos, conectores e outros componentes que possam afetar a precisão das medições.
Por fim, a falta de comunicação entre as equipes envolvidas no processo de calibração pode levar a erros. É importante que todos os profissionais envolvidos estejam cientes dos procedimentos, requisitos e expectativas em relação à calibração. A comunicação eficaz ajuda a garantir que todos estejam alinhados e que o processo de calibração seja realizado de forma consistente e precisa. Para evitar esse problema, as organizações devem promover uma cultura de comunicação aberta e colaboração entre as equipes, garantindo que todos os envolvidos estejam cientes de suas responsabilidades e do impacto de suas ações no processo de calibração.
Em resumo, a calibração de instrumentos de medição é um processo crítico que pode ser comprometido por diversos erros. A falta de padrões de referência adequados, condições inadequadas, falta de treinamento, documentação insuficiente, intervalos inadequados, ausência de verificação, uso de equipamentos danificados e falta de comunicação são alguns dos erros mais comuns que podem ocorrer. Ao identificar e abordar esses problemas, as organizações podem garantir que seus instrumentos de medição sejam calibrados corretamente, promovendo a precisão e a confiabilidade das medições realizadas.
Em conclusão, a calibração de instrumentos de medição é uma prática essencial que não apenas assegura a precisão e a confiabilidade das medições, mas também contribui para a qualidade e a segurança em diversos setores. A compreensão da importância da calibração, dos métodos adequados, da frequência recomendada e dos erros comuns que podem ocorrer é crucial para garantir que os instrumentos funcionem de maneira eficaz. Ao implementar práticas de calibração rigorosas e consistentes, as organizações podem minimizar riscos, otimizar processos e garantir a conformidade com normas e regulamentos. Investir em calibração é, portanto, um passo vital para qualquer empresa que busca excelência em suas operações e resultados.