Calibração de Instrumentos de Medição: Garantindo Precisão e Confiabilidade
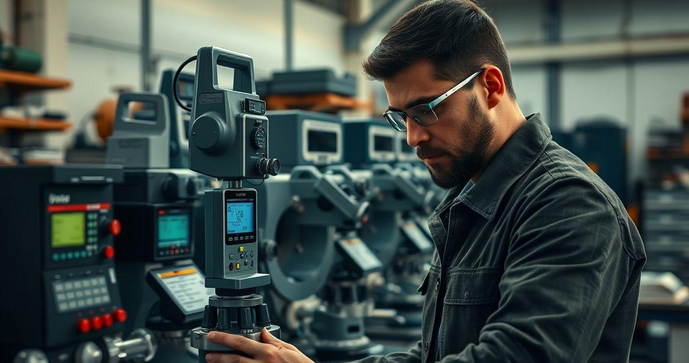
Por: Cláudio - 27 de Fevereiro de 2025
A calibração de instrumentos de medição é um processo fundamental para garantir a precisão e a confiabilidade dos resultados obtidos em diversas aplicações, desde laboratórios até ambientes industriais. Com a crescente demanda por qualidade e conformidade em processos produtivos, entender a importância da calibração se torna essencial. Neste artigo, abordaremos os principais aspectos relacionados à calibração de instrumentos de medição, incluindo métodos, frequência recomendada e erros comuns a serem evitados.
Importância da Calibração de Instrumentos de Medição na Indústria
A calibração de instrumentos de medição é um aspecto crucial na indústria, pois assegura que os equipamentos utilizados para medir, testar e controlar processos estejam funcionando com precisão. A precisão nas medições é vital para a qualidade do produto final, a segurança dos processos e a conformidade com normas regulatórias. Neste contexto, a calibração não é apenas uma prática recomendada, mas uma necessidade para garantir a eficiência operacional e a competitividade no mercado.
Um dos principais motivos para a calibração de instrumentos de medição é a garantia da qualidade. Em setores como farmacêutico, alimentício e químico, a precisão nas medições é fundamental para assegurar que os produtos atendam aos padrões de qualidade exigidos. Por exemplo, em uma linha de produção de medicamentos, a dosagem correta dos ingredientes ativos é essencial para a eficácia do produto. Qualquer desvio nas medições pode resultar em produtos ineficazes ou até mesmo perigosos, colocando em risco a saúde dos consumidores.
Além disso, a calibração contribui para a segurança operacional. Em indústrias onde equipamentos pesados e processos químicos são utilizados, medições imprecisas podem levar a acidentes graves. Por exemplo, em uma planta petroquímica, a medição correta de pressão e temperatura é vital para evitar explosões e vazamentos. A calibração regular dos instrumentos de medição ajuda a identificar e corrigir falhas antes que se tornem problemas sérios, garantindo um ambiente de trabalho seguro para os funcionários.
A conformidade com normas e regulamentos também é um fator importante que destaca a necessidade da calibração. Muitas indústrias são obrigadas a seguir normas específicas, como as estabelecidas pela ISO (Organização Internacional de Normalização) e pela ANVISA (Agência Nacional de Vigilância Sanitária). Essas normas frequentemente exigem que os instrumentos de medição sejam calibrados em intervalos regulares e que os resultados sejam documentados. A não conformidade pode resultar em penalidades, multas e até mesmo a suspensão das operações. Portanto, a calibração não apenas assegura a qualidade e a segurança, mas também protege as empresas de possíveis sanções legais.
Outro aspecto relevante é a eficiência operacional. Instrumentos de medição calibrados corretamente garantem que os processos industriais funcionem de maneira otimizada. Quando os instrumentos estão fora de calibração, pode haver desperdício de materiais, aumento de custos e redução da produtividade. Por exemplo, em uma linha de produção, a medição incorreta de ingredientes pode levar a lotes de produtos que não atendem às especificações, resultando em desperdício e retrabalho. A calibração regular ajuda a minimizar esses riscos, assegurando que os processos sejam executados de forma eficiente e econômica.
Além disso, a calibração de instrumentos de medição pode impactar diretamente a reputação da empresa. Em um mercado cada vez mais competitivo, a qualidade dos produtos e serviços oferecidos é um diferencial importante. Empresas que investem em calibração e garantem a precisão de suas medições são mais propensas a conquistar a confiança dos clientes e a se destacar no mercado. A reputação de uma empresa pode ser severamente afetada por problemas de qualidade, e a calibração é uma maneira eficaz de mitigar esses riscos.
Por fim, a calibração de instrumentos de medição é uma prática que deve ser incorporada à cultura organizacional das indústrias. Isso envolve não apenas a realização de calibrações regulares, mas também a formação e conscientização dos funcionários sobre a importância desse processo. Treinamentos e workshops podem ajudar a equipe a entender como a calibração afeta a qualidade e a segurança, promovendo um ambiente de trabalho mais responsável e comprometido com a excelência.
Em resumo, a calibração de instrumentos de medição é essencial para garantir a qualidade, segurança e eficiência operacional na indústria. Com a calibração, as empresas podem assegurar que seus produtos atendam aos padrões exigidos, proteger seus funcionários e evitar problemas legais. Além disso, a calibração contribui para a reputação da empresa e a confiança dos clientes. Para garantir a precisão das medições, é importante contar com serviços especializados, como a Calibração de balanças, que oferecem suporte técnico e garantem que os instrumentos estejam sempre em conformidade com as normas e padrões exigidos.
Métodos Comuns de Calibração de Instrumentos
A calibração de instrumentos de medição é um processo essencial para garantir a precisão e a confiabilidade dos resultados obtidos em diversas aplicações industriais e laboratoriais. Existem vários métodos de calibração que podem ser utilizados, dependendo do tipo de instrumento, da aplicação e dos requisitos específicos de cada setor. Neste artigo, abordaremos alguns dos métodos mais comuns de calibração de instrumentos, destacando suas características e aplicações.
Um dos métodos mais tradicionais de calibração é a calibração por comparação. Este método envolve a comparação do instrumento a ser calibrado com um padrão de referência que possui uma precisão conhecida. O instrumento de referência deve ser rastreável a padrões nacionais ou internacionais, garantindo a confiabilidade dos resultados. Durante o processo, o instrumento em teste é submetido a medições em diferentes pontos de operação, e os resultados são comparados com os valores do padrão. Qualquer desvio identificado pode ser ajustado, e a calibração é documentada para garantir a conformidade.
Outro método comum é a calibração por ajuste. Este método é frequentemente utilizado em instrumentos que possuem um mecanismo de ajuste interno, como manômetros e termômetros. Durante a calibração por ajuste, o instrumento é ajustado para que suas leituras correspondam aos valores do padrão de referência. Esse processo pode envolver a aplicação de uma força, temperatura ou pressão específica, dependendo do tipo de instrumento. A calibração por ajuste é especialmente útil para instrumentos que apresentam desvios sistemáticos, permitindo que sejam corrigidos de forma eficaz.
A calibração em campo é um método que se tornou cada vez mais popular, especialmente em indústrias onde a mobilidade dos instrumentos é essencial. Esse método envolve a calibração dos instrumentos diretamente no local de uso, em vez de enviá-los para um laboratório. A calibração em campo é vantajosa porque minimiza o tempo de inatividade dos equipamentos e permite que os técnicos realizem ajustes imediatos, se necessário. No entanto, é importante garantir que as condições ambientais durante a calibração sejam controladas, pois fatores como temperatura e umidade podem afetar os resultados.
Além disso, a calibração por simulação é um método que utiliza equipamentos de teste que simulam as condições de operação do instrumento. Esse método é frequentemente utilizado para instrumentos eletrônicos, como multímetros e osciloscópios. Durante a calibração por simulação, o instrumento é exposto a sinais de entrada conhecidos, e suas saídas são comparadas com os valores esperados. Esse método é eficaz para identificar não apenas desvios, mas também problemas de linearidade e resposta do instrumento. A calibração por simulação é especialmente útil em ambientes de laboratório, onde as condições podem ser controladas com precisão.
A calibração de torquímetro é um exemplo específico que ilustra a importância de métodos adequados de calibração. O torquímetro é um instrumento utilizado para medir a força de torque aplicada a um objeto, como parafusos e porcas. A Calibração de torquímetro é essencial para garantir que as medições de torque sejam precisas, evitando problemas como aperto excessivo ou insuficiente, que podem comprometer a integridade das montagens. A calibração de torquímetros geralmente envolve a aplicação de um torque conhecido e a verificação da leitura do instrumento, ajustando-o conforme necessário para garantir a precisão.
Outro método importante é a calibração por transferência. Este método é utilizado quando não é possível realizar a calibração diretamente no instrumento em teste. Em vez disso, um instrumento de referência é utilizado para medir um padrão de referência, e os resultados são transferidos para o instrumento em teste. Esse método é comum em laboratórios onde instrumentos de alta precisão são utilizados, e a calibração deve ser realizada em condições controladas. A calibração por transferência é uma maneira eficaz de garantir que os instrumentos estejam sempre em conformidade com os padrões exigidos.
Por fim, a calibração automática é uma tendência crescente na indústria, especialmente com o avanço da tecnologia. Instrumentos modernos frequentemente vêm equipados com recursos de calibração automática, que permitem que o próprio instrumento realize a calibração com base em padrões internos. Esse método pode economizar tempo e reduzir a necessidade de intervenção manual, mas ainda requer supervisão para garantir que os resultados sejam precisos e confiáveis.
Em resumo, a calibração de instrumentos de medição é um processo vital que garante a precisão e a confiabilidade das medições em diversas aplicações. Os métodos de calibração variam de acordo com o tipo de instrumento e as necessidades específicas de cada setor. A calibração por comparação, ajuste, em campo, simulação, transferência e automática são algumas das abordagens mais comuns utilizadas na indústria. Cada método tem suas vantagens e desvantagens, e a escolha do método adequado depende das circunstâncias e dos requisitos de cada situação. A implementação de práticas de calibração eficazes é fundamental para garantir a qualidade, segurança e eficiência operacional em qualquer ambiente industrial.
Frequência Recomendada para Calibração de Instrumentos de Medição
A calibração de instrumentos de medição é um processo essencial para garantir a precisão e a confiabilidade das medições em diversos setores, como industrial, farmacêutico e laboratorial. No entanto, a eficácia desse processo depende não apenas da qualidade dos instrumentos e dos métodos de calibração utilizados, mas também da frequência com que a calibração é realizada. Neste artigo, discutiremos a frequência recomendada para a calibração de instrumentos de medição, considerando fatores que influenciam essa periodicidade e a importância de manter um cronograma adequado.
A frequência de calibração pode variar significativamente dependendo do tipo de instrumento, da aplicação e das condições de uso. Em geral, instrumentos que são utilizados em ambientes críticos ou que realizam medições de alta precisão exigem calibrações mais frequentes. Por exemplo, instrumentos utilizados em laboratórios de controle de qualidade, onde a precisão é fundamental, podem necessitar de calibrações mensais ou trimestrais. Por outro lado, instrumentos que operam em condições menos rigorosas podem ser calibrados anualmente ou semestralmente.
Um dos principais fatores que influenciam a frequência de calibração é a estabilidade do instrumento. Instrumentos que apresentam uma tendência a desviar suas medições ao longo do tempo, como manômetros e termômetros, podem exigir calibrações mais frequentes. A estabilidade pode ser afetada por diversos fatores, incluindo condições ambientais, desgaste mecânico e uso inadequado. Portanto, é importante monitorar o desempenho do instrumento e ajustar a frequência de calibração conforme necessário.
Outro aspecto a ser considerado é a intensidade de uso do instrumento. Instrumentos que são utilizados com frequência em processos críticos, como a Calibração de válvula de segurança, podem exigir calibrações mais regulares. O uso constante pode levar a desgastes e variações nas medições, tornando a calibração uma necessidade para garantir a precisão. Em contrapartida, instrumentos que são utilizados esporadicamente podem ter uma frequência de calibração mais espaçada, desde que não apresentem sinais de desvio.
Além disso, a frequência de calibração deve ser influenciada pelas normas e regulamentos aplicáveis ao setor. Muitas indústrias são obrigadas a seguir diretrizes específicas que estabelecem a periodicidade das calibrações. Por exemplo, a ISO 9001, uma norma internacional de gestão da qualidade, recomenda que as organizações estabeleçam um cronograma de calibração baseado em critérios de risco e impacto. Portanto, é fundamental que as empresas estejam cientes das exigências regulatórias e ajustem suas práticas de calibração de acordo.
Outro fator importante a ser considerado é a experiência e o histórico de desempenho do instrumento. Se um instrumento tem um histórico de medições precisas e estáveis, pode ser possível estender o intervalo entre as calibrações. Por outro lado, se um instrumento frequentemente apresenta desvios ou falhas, pode ser necessário aumentar a frequência de calibração para garantir a confiabilidade das medições. A análise de dados históricos e a realização de testes de desempenho podem ajudar a determinar a frequência ideal de calibração.
Além disso, a calibração deve ser realizada sempre que ocorrerem mudanças significativas nas condições de operação. Por exemplo, se um instrumento for transferido para um novo ambiente com diferentes condições de temperatura ou umidade, é recomendável realizar uma calibração antes de colocá-lo em uso. Mudanças nas condições de operação podem afetar a precisão das medições e, portanto, a calibração é uma medida preventiva importante.
Por fim, é essencial que as empresas mantenham registros detalhados das calibrações realizadas, incluindo datas, resultados e quaisquer ajustes feitos. Esses registros não apenas ajudam a monitorar a frequência de calibração, mas também são importantes para auditorias e conformidade com normas regulatórias. A documentação adequada é uma parte fundamental do processo de calibração e deve ser mantida de forma organizada e acessível.
Em resumo, a frequência recomendada para a calibração de instrumentos de medição varia de acordo com diversos fatores, incluindo o tipo de instrumento, a intensidade de uso, as condições de operação e as exigências regulatórias. Instrumentos utilizados em ambientes críticos ou que apresentam instabilidade devem ser calibrados com mais frequência, enquanto aqueles em condições menos rigorosas podem ter intervalos mais longos. A manutenção de um cronograma de calibração adequado é essencial para garantir a precisão e a confiabilidade das medições, contribuindo para a qualidade e a segurança dos processos industriais e laboratoriais.
Erros Comuns na Calibração e Como Evitá-los
A calibração de instrumentos de medição é um processo crítico que garante a precisão e a confiabilidade das medições em diversos setores. No entanto, erros podem ocorrer durante esse processo, comprometendo a qualidade dos resultados. Neste artigo, discutiremos os erros comuns na calibração e como evitá-los, garantindo que os instrumentos funcionem de maneira eficaz e atendam aos padrões exigidos.
Um dos erros mais frequentes na calibração é a falta de um padrão de referência adequado. A calibração deve ser realizada em comparação com um padrão que tenha uma precisão conhecida e que seja rastreável a padrões nacionais ou internacionais. Quando um padrão inadequado é utilizado, as medições podem ser imprecisas, levando a resultados errôneos. Para evitar esse erro, é fundamental garantir que os padrões de referência utilizados sejam calibrados e certificados, além de estarem dentro do intervalo de medição do instrumento em teste.
Outro erro comum é a calibração em condições ambientais inadequadas. A temperatura, umidade e pressão atmosférica podem afetar significativamente as medições. Por exemplo, instrumentos eletrônicos podem apresentar variações em suas leituras se expostos a temperaturas extremas ou umidade excessiva. Para evitar esse problema, a calibração deve ser realizada em um ambiente controlado, onde as condições possam ser monitoradas e mantidas dentro dos limites especificados pelo fabricante do instrumento. Além disso, é importante permitir que o instrumento atinja a temperatura ambiente antes de iniciar o processo de calibração.
A falta de treinamento adequado para os operadores que realizam a calibração também é um fator que pode levar a erros. A calibração é um processo técnico que requer conhecimento e habilidades específicas. Operadores não treinados podem cometer erros ao seguir procedimentos de calibração, resultando em medições imprecisas. Para evitar esse problema, as empresas devem investir em treinamento contínuo para seus funcionários, garantindo que eles estejam atualizados sobre as melhores práticas e procedimentos de calibração. Além disso, a documentação clara dos procedimentos de calibração pode servir como um guia útil para os operadores.
Outro erro comum é a falta de manutenção adequada dos instrumentos de medição. Instrumentos que não são mantidos corretamente podem apresentar desvios em suas medições, tornando a calibração ineficaz. A manutenção regular, que inclui limpeza, lubrificação e verificação de componentes, é essencial para garantir que os instrumentos funcionem corretamente. As empresas devem estabelecer um cronograma de manutenção preventiva e garantir que todos os instrumentos sejam inspecionados e mantidos de acordo com as recomendações do fabricante.
A calibração em intervalos inadequados também pode ser um erro significativo. Se a calibração não for realizada com a frequência necessária, os instrumentos podem se desviar de suas especificações, resultando em medições imprecisas. Por outro lado, calibrações excessivas podem levar a desgaste desnecessário dos instrumentos. Para evitar esse erro, as empresas devem estabelecer um cronograma de calibração baseado em fatores como a intensidade de uso, as condições ambientais e as exigências regulatórias. A análise de dados históricos de desempenho dos instrumentos pode ajudar a determinar a frequência ideal de calibração.
Além disso, a falta de documentação adequada durante o processo de calibração pode levar a erros. Registros incompletos ou imprecisos podem dificultar a rastreabilidade e a verificação dos resultados de calibração. É fundamental que todas as etapas do processo de calibração sejam documentadas, incluindo os resultados das medições, os ajustes realizados e as condições ambientais durante a calibração. A documentação adequada não apenas ajuda a garantir a conformidade com as normas regulatórias, mas também serve como um recurso valioso para auditorias e revisões futuras.
Outro erro que pode ocorrer é a falta de verificação pós-calibração. Após a calibração, é importante realizar testes adicionais para garantir que o instrumento esteja funcionando corretamente e que as medições estejam dentro das especificações. A verificação pós-calibração pode incluir a realização de medições em pontos de referência conhecidos e a comparação dos resultados com os valores esperados. Essa etapa é crucial para identificar quaisquer problemas que possam ter surgido durante o processo de calibração.
Por fim, a escolha inadequada de uma empresa de calibração de instrumentos de medição pode resultar em erros significativos. É essencial selecionar um prestador de serviços que tenha experiência e credibilidade no setor. A empresa deve ser capaz de fornecer documentação adequada, garantir a rastreabilidade dos padrões utilizados e seguir as melhores práticas de calibração. A pesquisa e a verificação de referências podem ajudar a garantir que a empresa escolhida atenda a todos os requisitos necessários.
Em resumo, a calibração de instrumentos de medição é um processo crítico que deve ser realizado com cuidado e atenção. Erros comuns, como a falta de padrões adequados, condições ambientais inadequadas, falta de treinamento, manutenção insuficiente, calibrações em intervalos inadequados, documentação deficiente, falta de verificação pós-calibração e a escolha inadequada de prestadores de serviços podem comprometer a precisão das medições. Ao estar ciente desses erros e implementar medidas para evitá-los, as empresas podem garantir que seus instrumentos de medição funcionem de maneira eficaz e atendam aos padrões exigidos.
Em conclusão, a calibração de instrumentos de medição é uma prática indispensável que assegura a precisão e a confiabilidade das medições em diversos setores. A compreensão dos métodos de calibração, a definição de uma frequência adequada e a conscientização sobre os erros comuns que podem ocorrer são passos cruciais para garantir a qualidade dos processos. Ao implementar práticas eficazes de calibração e evitar erros, as empresas não apenas melhoram a eficiência operacional, mas também garantem a conformidade com normas regulatórias e a segurança dos produtos e serviços oferecidos. Investir em calibração é, portanto, um investimento na qualidade e na reputação da organização.