Calibração de Instrumentos de Medição é Essencial para Garantir Precisão e Confiabilidade
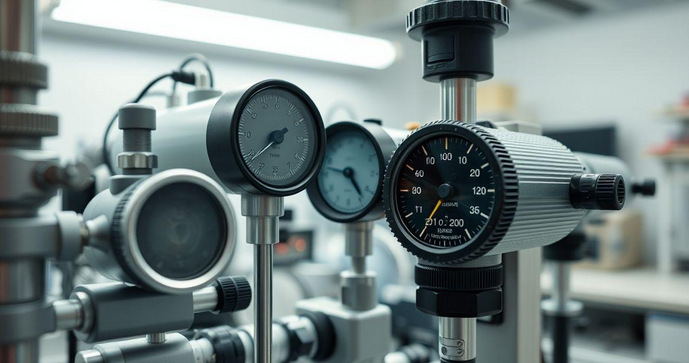
Por: Cláudio - 15 de Março de 2025
A calibração de instrumentos de medição é um processo fundamental para garantir a precisão e a confiabilidade dos dados obtidos em diversas aplicações, desde laboratórios até ambientes industriais. Com a crescente demanda por qualidade e conformidade em processos, entender a importância da calibração se torna essencial para profissionais e empresas. Neste artigo, abordaremos os métodos, a frequência recomendada e os erros comuns na calibração, proporcionando um guia completo para otimizar a precisão dos instrumentos de medição.
Importância da Calibração de Instrumentos de Medição na Indústria
A calibração de instrumentos de medição é um aspecto crucial em diversos setores industriais, pois garante que os equipamentos estejam funcionando de acordo com padrões estabelecidos. A precisão nas medições é vital para a qualidade dos produtos, segurança dos processos e conformidade com regulamentações. Neste contexto, a calibração não é apenas uma prática recomendada, mas uma necessidade para assegurar a integridade das operações industriais.
Um dos principais motivos para a calibração de instrumentos de medição é a prevenção de erros que podem resultar em produtos defeituosos. Em indústrias como a farmacêutica, alimentícia e de manufatura, a precisão nas medições é fundamental. Por exemplo, em uma linha de produção de medicamentos, a dosagem correta de ingredientes ativos é essencial para garantir a eficácia e a segurança do produto final. Um pequeno erro na medição pode levar a consequências graves, incluindo riscos à saúde dos consumidores e prejuízos financeiros para a empresa.
Além disso, a calibração ajuda a manter a conformidade com normas e regulamentos. Muitas indústrias são obrigadas a seguir padrões específicos, como as normas ISO, que exigem que os instrumentos de medição sejam calibrados regularmente. A não conformidade pode resultar em multas, sanções e até mesmo a suspensão das operações. Portanto, a calibração não apenas assegura a qualidade do produto, mas também protege a empresa de possíveis penalidades legais.
Outro aspecto importante da calibração é a melhoria da eficiência operacional. Instrumentos de medição que não estão calibrados corretamente podem levar a retrabalhos, desperdício de materiais e tempo. Por exemplo, em uma fábrica de alimentos, se a balança utilizada para pesar ingredientes não estiver calibrada, pode resultar em quantidades incorretas, levando a um produto final que não atende aos padrões de qualidade. Isso não apenas afeta a satisfação do cliente, mas também pode resultar em perdas financeiras significativas.
A calibração de instrumentos de medição também é essencial para a segurança no ambiente de trabalho. Em indústrias onde a medição precisa de pressão, temperatura ou outros parâmetros críticos, um instrumento não calibrado pode levar a falhas catastróficas. Por exemplo, em uma planta química, a medição incorreta de pressão em um reator pode resultar em explosões ou vazamentos perigosos. Portanto, garantir que os instrumentos estejam calibrados é uma questão de segurança para os trabalhadores e para a comunidade ao redor.
Além disso, a calibração contribui para a confiança nas medições. Quando os instrumentos são calibrados regularmente, as empresas podem ter certeza de que os dados coletados são precisos e confiáveis. Isso é especialmente importante em setores onde a rastreabilidade é necessária, como na indústria automotiva e aeroespacial. A capacidade de demonstrar que as medições atendem a padrões específicos é fundamental para a credibilidade da empresa e para a confiança dos clientes.
Outro ponto a ser considerado é a calibração de balanças, que é uma prática comum em muitas indústrias. A Calibração de balanças é essencial para garantir que os pesos medidos estejam corretos, evitando discrepâncias que podem afetar a produção e a qualidade do produto. Balanças não calibradas podem resultar em erros de pesagem, que podem comprometer a integridade do produto final e a satisfação do cliente.
Além disso, a calibração deve ser realizada por profissionais qualificados e em ambientes controlados, utilizando padrões de referência que garantam a precisão das medições. A escolha de um laboratório de calibração confiável é fundamental para assegurar que os instrumentos atendam aos requisitos necessários. Muitas empresas optam por terceirizar esse serviço, garantindo que a calibração seja realizada de acordo com as melhores práticas do setor.
Por fim, a calibração de instrumentos de medição é uma prática que deve ser incorporada à cultura organizacional das indústrias. A conscientização sobre a importância da calibração deve ser disseminada entre todos os colaboradores, desde a alta gestão até os operadores de máquinas. Investir em treinamento e capacitação é fundamental para garantir que todos compreendam a relevância da calibração e suas implicações para a qualidade e segurança dos produtos.
Em resumo, a calibração de instrumentos de medição é vital para a indústria, pois assegura a precisão, conformidade, eficiência operacional e segurança. A prática regular de calibração não apenas protege a empresa de riscos legais e financeiros, mas também contribui para a confiança dos clientes e a qualidade dos produtos. Portanto, é essencial que as indústrias adotem uma abordagem proativa em relação à calibração, garantindo que seus instrumentos estejam sempre em conformidade com os padrões exigidos.
Métodos Comuns de Calibração de Instrumentos
A calibração de instrumentos de medição é um processo essencial para garantir a precisão e a confiabilidade dos dados obtidos em diversas aplicações. Existem vários métodos de calibração que podem ser utilizados, dependendo do tipo de instrumento, da aplicação e dos requisitos específicos de cada setor. Neste artigo, abordaremos alguns dos métodos mais comuns de calibração de instrumentos, destacando suas características e aplicações.
Um dos métodos mais tradicionais de calibração é a calibração por comparação. Neste método, o instrumento a ser calibrado é comparado a um padrão de referência conhecido, que possui uma precisão superior. O instrumento é submetido a medições em condições controladas, e os resultados são comparados com os valores do padrão. Essa abordagem é amplamente utilizada em laboratórios de metrologia e é eficaz para garantir que os instrumentos estejam dentro das especificações exigidas.
Outro método comum é a calibração por ajuste. Neste caso, o instrumento é ajustado para que suas medições correspondam aos valores do padrão de referência. Esse método é frequentemente utilizado em instrumentos que apresentam desvios sistemáticos, permitindo que os operadores ajustem o equipamento para garantir medições precisas. A calibração por ajuste é comum em instrumentos como balanças, termômetros e manômetros, onde a precisão é crítica.
A calibração em campo é um método que se tornou cada vez mais popular, especialmente em indústrias que utilizam instrumentos móveis ou que operam em locais remotos. Neste método, os instrumentos são calibrados no local de uso, utilizando padrões de referência portáteis. A calibração em campo é vantajosa porque permite que os instrumentos sejam verificados e ajustados sem a necessidade de serem enviados para um laboratório, economizando tempo e recursos. No entanto, é importante garantir que as condições ambientais sejam controladas para evitar influências externas que possam afetar os resultados.
Além disso, a calibração por simulação é um método que utiliza equipamentos de teste que simulam as condições de operação do instrumento. Esse método é especialmente útil para instrumentos que não podem ser calibrados diretamente, como sensores de pressão ou temperatura. A calibração por simulação permite que os operadores verifiquem o desempenho do instrumento em condições específicas, garantindo que ele funcione corretamente em situações reais.
Outro método importante é a Calibração de torquímetro, que é essencial em indústrias onde a aplicação de torque é crítica, como na montagem de peças automotivas e na construção. A calibração de torquímetros envolve a aplicação de um torque conhecido ao instrumento e a verificação de sua leitura. Esse método garante que o torquímetro esteja fornecendo medições precisas, evitando falhas na montagem e garantindo a segurança dos produtos finais.
A calibração de instrumentos eletrônicos, como multímetros e osciloscópios, também é um aspecto importante da metrologia. Esses instrumentos são calibrados utilizando padrões de tensão, corrente e frequência conhecidos. A calibração é realizada em condições controladas, e os resultados são registrados para garantir a rastreabilidade. A precisão desses instrumentos é fundamental em aplicações eletrônicas, onde pequenas variações podem ter um impacto significativo no desempenho dos sistemas.
Outro método de calibração é a calibração por ponto fixo, que envolve a medição de um ou mais pontos específicos em um intervalo de operação. Esse método é frequentemente utilizado em termômetros e manômetros, onde a precisão em pontos críticos é essencial. A calibração por ponto fixo permite que os operadores verifiquem a precisão do instrumento em condições específicas, garantindo que ele funcione corretamente em toda a sua faixa de operação.
Além dos métodos mencionados, a calibração por transferência é uma abordagem que envolve o uso de um instrumento calibrado para verificar outro instrumento. Esse método é útil quando não é possível utilizar um padrão de referência direto. A calibração por transferência é comum em ambientes industriais, onde a disponibilidade de padrões de referência pode ser limitada.
Por fim, a calibração deve ser realizada por profissionais qualificados e em ambientes controlados, utilizando padrões de referência que garantam a precisão das medições. A escolha de um laboratório de calibração confiável é fundamental para assegurar que os instrumentos atendam aos requisitos necessários. Muitas empresas optam por terceirizar esse serviço, garantindo que a calibração seja realizada de acordo com as melhores práticas do setor.
Em resumo, existem diversos métodos de calibração de instrumentos de medição, cada um com suas características e aplicações específicas. A escolha do método adequado depende do tipo de instrumento, das condições de operação e dos requisitos de precisão. A calibração regular é essencial para garantir a confiabilidade das medições e a qualidade dos produtos, contribuindo para a segurança e eficiência das operações industriais.
Frequência Recomendada para Calibração de Instrumentos de Medição
A calibração de instrumentos de medição é um processo essencial para garantir a precisão e a confiabilidade dos dados obtidos em diversas aplicações. No entanto, a eficácia desse processo depende não apenas da qualidade da calibração em si, mas também da frequência com que ela é realizada. A determinação da frequência recomendada para calibração é um aspecto crítico que pode variar de acordo com o tipo de instrumento, a aplicação e as condições de uso. Neste artigo, discutiremos a importância da frequência de calibração e as diretrizes gerais que podem ser seguidas.
Um dos principais fatores que influenciam a frequência de calibração é a natureza do instrumento e sua aplicação. Instrumentos utilizados em ambientes críticos, como laboratórios de pesquisa, indústrias farmacêuticas e alimentícias, geralmente exigem calibrações mais frequentes. Isso se deve ao fato de que, nessas indústrias, a precisão das medições é vital para garantir a qualidade e a segurança dos produtos. Por exemplo, a Calibração de válvula de segurança deve ser realizada regularmente para garantir que os dispositivos funcionem corretamente e protejam os sistemas contra sobrepressão, evitando acidentes e danos ao equipamento.
Além disso, a frequência de calibração pode ser influenciada pela intensidade de uso do instrumento. Instrumentos que são utilizados com frequência ou que estão sujeitos a condições adversas, como vibrações, temperaturas extremas ou umidade, podem apresentar desvios mais rapidamente. Nesses casos, recomenda-se uma calibração mais frequente para garantir que os instrumentos permaneçam dentro das especificações. Por outro lado, instrumentos que são utilizados com menos frequência podem ter uma frequência de calibração mais espaçada.
Outro aspecto a ser considerado é a estabilidade do instrumento. Alguns instrumentos são projetados para manter sua precisão ao longo do tempo, enquanto outros podem ser mais suscetíveis a variações. A estabilidade pode ser afetada por fatores como desgaste mecânico, exposição a condições ambientais adversas e envelhecimento dos componentes. Portanto, é importante monitorar o desempenho do instrumento e ajustar a frequência de calibração conforme necessário.
As diretrizes de calibração frequentemente recomendam que a frequência de calibração seja estabelecida com base em uma combinação de fatores, incluindo a experiência anterior com o instrumento, as recomendações do fabricante e as normas aplicáveis. Muitas organizações seguem as diretrizes da ISO 9001, que sugere que a calibração deve ser realizada em intervalos regulares, mas também deve levar em consideração a criticidade do instrumento e o impacto que medições imprecisas podem ter nos processos.
Além disso, a realização de auditorias internas e a análise de dados históricos de desempenho podem ajudar a determinar a frequência ideal de calibração. Se um instrumento apresentar desvios frequentes ou inconsistências nas medições, pode ser necessário aumentar a frequência de calibração. Por outro lado, se um instrumento demonstrar um desempenho estável ao longo do tempo, a frequência de calibração pode ser reduzida.
É importante ressaltar que a calibração não deve ser vista apenas como uma tarefa a ser realizada em intervalos fixos, mas sim como parte de um sistema de gestão da qualidade. A implementação de um programa de manutenção preventiva que inclua a calibração regular pode ajudar a identificar problemas antes que eles se tornem críticos, garantindo que os instrumentos estejam sempre em conformidade com os padrões exigidos.
Além disso, a documentação adequada das calibrações realizadas é fundamental. Registros detalhados devem ser mantidos, incluindo a data da calibração, os resultados obtidos, as ações corretivas tomadas e a próxima data programada para calibração. Essa documentação não apenas ajuda a garantir a rastreabilidade, mas também fornece informações valiosas para a análise de tendências e a tomada de decisões sobre a frequência de calibração.
Por fim, a formação e a conscientização dos colaboradores sobre a importância da calibração e da frequência recomendada são essenciais. Todos os envolvidos no processo de medição devem entender a relevância da calibração e como ela impacta a qualidade dos produtos e a segurança dos processos. Investir em treinamento e capacitação pode ajudar a criar uma cultura de qualidade dentro da organização, onde a calibração é vista como uma prioridade.
Em resumo, a frequência recomendada para calibração de instrumentos de medição deve ser determinada com base em uma combinação de fatores, incluindo a natureza do instrumento, a intensidade de uso, a estabilidade e as diretrizes do fabricante. A calibração regular é essencial para garantir a precisão e a confiabilidade das medições, contribuindo para a qualidade dos produtos e a segurança dos processos. Implementar um programa de calibração eficaz e manter registros detalhados são práticas fundamentais para garantir que os instrumentos estejam sempre em conformidade com os padrões exigidos.
Erros Comuns na Calibração e Como Evitá-los
A calibração de instrumentos de medição é um processo crítico que garante a precisão e a confiabilidade das medições em diversas aplicações. No entanto, erros podem ocorrer durante esse processo, comprometendo a qualidade dos resultados. Identificar e evitar esses erros é fundamental para garantir que os instrumentos funcionem corretamente e atendam aos padrões exigidos. Neste artigo, discutiremos alguns dos erros mais comuns na calibração e como evitá-los.
Um dos erros mais frequentes na calibração é a falta de um padrão de referência adequado. A calibração deve ser realizada utilizando padrões que sejam rastreáveis a unidades de medida reconhecidas nacional ou internacionalmente. Se o padrão de referência não for adequado, as medições do instrumento calibrado podem estar incorretas. Para evitar esse erro, é essencial utilizar padrões de calibração que sejam certificados e que atendam às especificações necessárias para o tipo de instrumento em questão.
Outro erro comum é a calibração em condições inadequadas. A temperatura, umidade e pressão atmosférica podem afetar significativamente os resultados da calibração. Por exemplo, calibrar um instrumento em um ambiente com variações extremas de temperatura pode levar a medições imprecisas. Para evitar esse problema, é importante realizar a calibração em um ambiente controlado, onde as condições possam ser monitoradas e mantidas dentro dos limites especificados pelo fabricante do instrumento.
A falta de treinamento adequado dos profissionais que realizam a calibração também é um fator que pode levar a erros. A calibração requer conhecimento técnico e habilidades específicas para garantir que os procedimentos sejam seguidos corretamente. Profissionais não treinados podem cometer erros ao ajustar os instrumentos ou interpretar os resultados. Para evitar esse problema, as empresas devem investir em treinamento contínuo para suas equipes, garantindo que todos os envolvidos no processo de calibração estejam atualizados sobre as melhores práticas e procedimentos.
Além disso, a falta de documentação adequada pode resultar em erros na calibração. Registros detalhados das calibrações realizadas, incluindo os resultados, as condições em que foram feitas e as ações corretivas tomadas, são essenciais para garantir a rastreabilidade e a conformidade. Sem documentação adequada, pode ser difícil identificar problemas ou justificar a precisão das medições. Para evitar esse erro, as empresas devem implementar um sistema de gerenciamento de documentos que permita o registro e a manutenção de informações relevantes sobre as calibrações.
Outro erro comum é a calibração de instrumentos que não estão em condições adequadas de funcionamento. Antes de realizar a calibração, é importante verificar se o instrumento está limpo, livre de danos e funcionando corretamente. Se um instrumento estiver com defeito, a calibração não será eficaz e poderá resultar em medições imprecisas. Para evitar esse problema, as empresas devem estabelecer procedimentos de verificação pré-calibração que garantam que os instrumentos estejam prontos para o processo de calibração.
A calibração em intervalos inadequados também é um erro que pode comprometer a precisão das medições. A frequência de calibração deve ser determinada com base em fatores como a intensidade de uso, as condições ambientais e as recomendações do fabricante. Se a calibração for realizada com muita frequência, pode resultar em custos desnecessários, enquanto calibrações realizadas com pouca frequência podem levar a medições imprecisas. Para evitar esse erro, as empresas devem estabelecer um cronograma de calibração que leve em consideração todos esses fatores e que seja revisado regularmente.
Além disso, a falta de comunicação entre as equipes envolvidas no processo de calibração pode resultar em erros. É fundamental que todos os envolvidos, desde os operadores até os técnicos de calibração, estejam cientes dos procedimentos e das expectativas. A falta de comunicação pode levar a mal-entendidos e, consequentemente, a erros na calibração. Para evitar esse problema, as empresas devem promover uma cultura de comunicação aberta e colaboração entre as equipes, garantindo que todos estejam alinhados em relação aos objetivos e procedimentos de calibração.
Por fim, a escolha inadequada de uma empresa de calibração de instrumentos de medição pode resultar em erros significativos. É importante selecionar um fornecedor confiável e experiente, que siga as melhores práticas e normas do setor. A falta de credibilidade do fornecedor pode comprometer a qualidade da calibração e, consequentemente, a precisão das medições. Para evitar esse erro, as empresas devem realizar uma pesquisa cuidadosa ao escolher um fornecedor de calibração, verificando suas credenciais, certificações e histórico de desempenho.
Em resumo, a calibração de instrumentos de medição é um processo crítico que pode ser afetado por diversos erros. A falta de um padrão de referência adequado, condições inadequadas, falta de treinamento, documentação insuficiente, calibração de instrumentos defeituosos, intervalos inadequados, falta de comunicação e escolha inadequada de fornecedores são alguns dos erros mais comuns. Ao identificar e evitar esses erros, as empresas podem garantir a precisão e a confiabilidade das medições, contribuindo para a qualidade dos produtos e a segurança dos processos.
Em conclusão, a calibração de instrumentos de medição é uma prática indispensável para assegurar a qualidade e a segurança em diversos setores. A compreensão dos métodos de calibração, a definição de uma frequência adequada e a identificação de erros comuns são passos cruciais para garantir que os instrumentos operem com precisão. Ao implementar um programa de calibração eficaz e seguir as melhores práticas, profissionais e empresas podem não apenas atender às exigências regulatórias, mas também melhorar a eficiência operacional e a confiança nos resultados obtidos. Investir na calibração é, portanto, um investimento na qualidade e na excelência dos processos, refletindo diretamente na satisfação do cliente e no sucesso do negócio.