Calibração de Equipamentos: Garantindo Precisão e Confiabilidade em Seus Processos
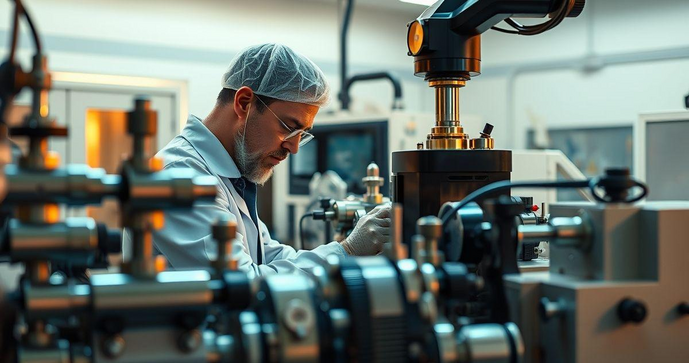
Por: Cláudio - 27 de Fevereiro de 2025
A calibração de equipamentos é um processo fundamental para garantir a precisão e a confiabilidade das medições em diversos setores, como industrial, laboratorial e de saúde. Este procedimento assegura que os instrumentos estejam funcionando dentro dos padrões estabelecidos, evitando erros que podem comprometer a qualidade dos produtos e serviços. Neste artigo, abordaremos a importância da calibração, os métodos utilizados, a frequência recomendada e os erros comuns que devem ser evitados.
Importância da Calibração de Equipamentos na Indústria
A calibração de equipamentos é um aspecto crucial na indústria, pois garante que os instrumentos de medição estejam funcionando corretamente e dentro dos padrões estabelecidos. A precisão nas medições é vital para a qualidade dos produtos, a segurança dos processos e a conformidade com as normas regulatórias. Neste contexto, a calibração não é apenas uma prática recomendada, mas uma necessidade para manter a competitividade e a eficiência operacional.
Um dos principais motivos para a calibração de equipamentos é a garantia da qualidade do produto final. Em setores como farmacêutico, alimentício e de manufatura, a precisão nas medições pode impactar diretamente a segurança e a eficácia dos produtos. Por exemplo, em uma linha de produção de medicamentos, a dosagem correta dos ingredientes ativos é essencial. Qualquer desvio pode resultar em produtos ineficazes ou até mesmo perigosos. Portanto, a calibração regular dos equipamentos de medição é fundamental para assegurar que os produtos atendam aos padrões de qualidade exigidos.
Além disso, a calibração de equipamentos ajuda a evitar desperdícios e retrabalhos. Quando os instrumentos não estão calibrados corretamente, as medições podem estar imprecisas, levando a erros na produção. Isso pode resultar em materiais desperdiçados, tempo perdido e custos adicionais. Por outro lado, ao garantir que os equipamentos estejam calibrados, as indústrias podem otimizar seus processos, reduzindo custos e aumentando a eficiência. A calibração, portanto, não é apenas uma questão de conformidade, mas uma estratégia de negócios que pode impactar diretamente a rentabilidade.
A calibração também é essencial para a conformidade com normas e regulamentos. Muitas indústrias são obrigadas a seguir padrões específicos estabelecidos por órgãos reguladores, como a ANVISA no Brasil ou a FDA nos Estados Unidos. Esses regulamentos frequentemente exigem que os equipamentos de medição sejam calibrados regularmente para garantir a precisão e a confiabilidade dos resultados. O não cumprimento dessas normas pode resultar em penalidades, multas e até mesmo a suspensão das operações. Portanto, a calibração é uma parte integral da estratégia de conformidade das empresas.
Outro aspecto importante da calibração de equipamentos é a segurança. Em indústrias onde a segurança é uma preocupação primordial, como a petroquímica e a de construção, a precisão nas medições pode ser a diferença entre um ambiente de trabalho seguro e um potencial desastre. Equipamentos de medição imprecisos podem levar a decisões erradas, que podem resultar em acidentes graves. A calibração regular ajuda a mitigar esses riscos, garantindo que os instrumentos estejam sempre prontos para fornecer dados precisos e confiáveis.
Além disso, a calibração de equipamentos pode contribuir para a melhoria contínua dos processos industriais. Ao monitorar e calibrar regularmente os instrumentos, as empresas podem identificar tendências e padrões que podem indicar a necessidade de ajustes nos processos. Isso não apenas ajuda a manter a qualidade, mas também pode levar a inovações e melhorias que aumentam a eficiência e a competitividade no mercado.
É importante ressaltar que a calibração deve ser realizada por profissionais qualificados e em ambientes adequados. A escolha de um laboratório de calibração confiável é fundamental para garantir que os equipamentos sejam calibrados de acordo com os padrões exigidos. Por exemplo, a Calibração de balanças é um serviço especializado que deve ser realizado por técnicos experientes, utilizando equipamentos de alta precisão e seguindo procedimentos rigorosos.
Em resumo, a calibração de equipamentos na indústria é uma prática essencial que impacta diretamente a qualidade do produto, a eficiência operacional, a conformidade regulatória e a segurança. As empresas que investem na calibração regular de seus instrumentos não apenas garantem a precisão das medições, mas também se posicionam de forma competitiva no mercado. A calibração deve ser vista como um investimento estratégico, que traz benefícios a longo prazo e contribui para o sucesso das operações industriais.
Portanto, a implementação de um programa de calibração eficaz é fundamental para qualquer empresa que busca manter altos padrões de qualidade e eficiência. A calibração não é apenas uma tarefa a ser realizada, mas uma parte integrante da cultura de qualidade de uma organização. Ao priorizar a calibração de equipamentos, as indústrias podem garantir que estão sempre operando em seu melhor desempenho, atendendo às expectativas dos clientes e cumprindo com as exigências do mercado.
Métodos Comuns de Calibração de Equipamentos
A calibração de equipamentos é um processo essencial para garantir a precisão e a confiabilidade das medições em diversos setores industriais. Existem vários métodos de calibração que podem ser aplicados, dependendo do tipo de equipamento e das especificações necessárias. Neste artigo, abordaremos alguns dos métodos mais comuns de calibração de equipamentos, destacando suas características e aplicações.
Um dos métodos mais utilizados é a calibração por comparação. Este método envolve a comparação do equipamento a ser calibrado com um padrão de referência que possui uma precisão conhecida. O equipamento de referência deve ser calibrado e rastreável a padrões nacionais ou internacionais. Durante o processo, o equipamento em teste é submetido a medições em condições controladas, e os resultados são comparados com os valores do padrão. Essa abordagem é amplamente utilizada em laboratórios e indústrias, pois permite identificar desvios e ajustar o equipamento conforme necessário.
Outro método comum é a calibração por ajuste. Neste caso, o equipamento é ajustado diretamente para atender às especificações desejadas. Isso é feito utilizando dispositivos de ajuste que permitem modificar a saída do equipamento até que ela corresponda ao padrão de referência. Este método é frequentemente utilizado em instrumentos de medição que possuem mecanismos de ajuste interno, como manômetros e termômetros. A calibração por ajuste é eficaz, mas deve ser realizada com cuidado para evitar danos ao equipamento.
A calibração em campo é um método que se tornou cada vez mais popular, especialmente em indústrias que utilizam equipamentos móveis ou que operam em locais remotos. Neste método, os técnicos realizam a calibração diretamente no local de uso do equipamento. Isso é particularmente útil para instrumentos que não podem ser facilmente transportados para um laboratório de calibração. A calibração em campo geralmente envolve a utilização de padrões portáteis e equipamentos de medição que permitem verificar a precisão do instrumento em condições reais de operação.
Além disso, a calibração por simulação é um método que utiliza dispositivos de simulação para reproduzir as condições de operação do equipamento. Este método é frequentemente utilizado em equipamentos eletrônicos e de comunicação, onde as medições podem ser complexas e dependem de variáveis específicas. A calibração por simulação permite que os técnicos verifiquem o desempenho do equipamento em uma variedade de condições, garantindo que ele funcione corretamente em situações reais.
Outro método importante é a calibração por transferência. Este método é utilizado quando não é possível realizar a calibração direta do equipamento em teste. Em vez disso, um equipamento de referência é utilizado para transferir as características de calibração para o equipamento em teste. Isso é comum em situações onde o equipamento em teste é muito grande ou pesado para ser transportado. A calibração por transferência é uma solução prática que permite garantir a precisão sem a necessidade de mover o equipamento.
Um exemplo específico de calibração é a Calibração de torquímetro, que é essencial para garantir que as medições de torque estejam dentro das especificações corretas. Os torquímetros são amplamente utilizados em aplicações que exigem a aplicação precisa de torque, como na montagem de peças em automóveis e equipamentos industriais. A calibração adequada desses instrumentos é crucial para evitar falhas na montagem e garantir a segurança dos produtos finais.
Além dos métodos mencionados, a calibração por comparação de múltiplos pontos é uma técnica que envolve a verificação do equipamento em vários pontos de medição. Isso é especialmente útil para instrumentos que operam em uma faixa ampla de medições, como balanças e medidores de pressão. Ao calibrar em múltiplos pontos, os técnicos podem identificar não apenas desvios em um ponto específico, mas também tendências que podem indicar problemas em toda a faixa de operação do equipamento.
Por fim, a calibração automática é uma tendência crescente, especialmente com o avanço da tecnologia. Equipamentos modernos podem ser projetados para realizar calibrações automáticas, utilizando sensores e algoritmos para ajustar suas medições em tempo real. Isso não apenas aumenta a precisão, mas também reduz a necessidade de intervenção manual, economizando tempo e recursos. A calibração automática é particularmente vantajosa em ambientes industriais onde a eficiência é crucial.
Em resumo, existem diversos métodos de calibração de equipamentos, cada um com suas características e aplicações específicas. A escolha do método adequado depende do tipo de equipamento, das condições de operação e das necessidades de precisão. A calibração regular e eficaz é fundamental para garantir a qualidade dos produtos e a segurança dos processos industriais. Ao entender os métodos disponíveis, as empresas podem implementar práticas de calibração que atendam às suas necessidades e mantenham seus equipamentos em conformidade com os padrões exigidos.
Frequência Recomendada para Calibração de Equipamentos
A calibração de equipamentos é um processo essencial para garantir a precisão e a confiabilidade das medições em diversos setores industriais. No entanto, a eficácia desse processo depende não apenas da qualidade da calibração em si, mas também da frequência com que ela é realizada. Neste artigo, discutiremos a frequência recomendada para a calibração de equipamentos, considerando diferentes fatores que podem influenciar essa necessidade.
Em primeiro lugar, é importante entender que a frequência de calibração pode variar significativamente de acordo com o tipo de equipamento e sua aplicação. Equipamentos que operam em ambientes críticos, como laboratórios de pesquisa, indústrias farmacêuticas e de alimentos, geralmente exigem calibrações mais frequentes. Isso se deve ao fato de que pequenas variações nas medições podem ter consequências graves, como a produção de produtos inseguros ou ineficazes. Portanto, para esses setores, recomenda-se que a calibração seja realizada pelo menos uma vez a cada seis meses.
Por outro lado, equipamentos utilizados em ambientes menos críticos podem ter uma frequência de calibração mais espaçada. Por exemplo, instrumentos de medição utilizados em processos de controle de qualidade em fábricas podem ser calibrados anualmente, desde que os resultados das medições estejam dentro dos limites aceitáveis. No entanto, é fundamental que as empresas realizem uma avaliação contínua do desempenho dos equipamentos para determinar se a frequência de calibração deve ser ajustada.
Outro fator a ser considerado é a intensidade de uso do equipamento. Equipamentos que são utilizados com frequência e em condições severas, como altas temperaturas, umidade ou vibrações, tendem a sofrer desgastes mais rapidamente. Nesses casos, a calibração deve ser realizada com maior frequência, podendo ser trimestral ou até mensal, dependendo da criticidade do processo. Por exemplo, a Calibração de válvula de segurança é um procedimento que deve ser realizado regularmente, pois a precisão dessas válvulas é crucial para a segurança operacional em indústrias químicas e petroquímicas.
Além disso, a frequência de calibração também pode ser influenciada por mudanças nas condições de operação. Se um equipamento for transferido para um novo ambiente ou se as condições de operação mudarem significativamente, é recomendável realizar uma calibração imediata. Isso garante que o equipamento continue a operar dentro dos padrões exigidos e que as medições permaneçam precisas. Mudanças nas condições de operação podem incluir alterações na temperatura, umidade, pressão ou até mesmo na qualidade dos materiais utilizados.
As normas e regulamentos aplicáveis ao setor também desempenham um papel importante na determinação da frequência de calibração. Muitas indústrias são obrigadas a seguir diretrizes específicas estabelecidas por órgãos reguladores, que podem incluir requisitos de calibração. Por exemplo, a indústria farmacêutica deve seguir as diretrizes da ANVISA, que frequentemente exigem calibrações regulares para garantir a qualidade e a segurança dos produtos. Portanto, as empresas devem estar cientes das regulamentações que se aplicam ao seu setor e garantir que suas práticas de calibração estejam em conformidade.
Além disso, a análise de dados históricos de desempenho do equipamento pode fornecer insights valiosos sobre a frequência de calibração necessária. Se um equipamento apresentar resultados consistentes e dentro dos limites aceitáveis ao longo do tempo, pode ser possível estender o intervalo entre as calibrações. No entanto, essa decisão deve ser baseada em dados concretos e não em suposições. A implementação de um sistema de monitoramento contínuo pode ajudar as empresas a coletar dados relevantes e tomar decisões informadas sobre a calibração.
Por fim, é importante ressaltar que a calibração não deve ser vista apenas como uma tarefa a ser realizada, mas como parte integrante da cultura de qualidade de uma organização. As empresas que priorizam a calibração regular de seus equipamentos não apenas garantem a precisão das medições, mas também se posicionam de forma competitiva no mercado. A calibração deve ser considerada um investimento estratégico que traz benefícios a longo prazo, como a redução de desperdícios, a melhoria da qualidade do produto e a conformidade com as normas regulatórias.
Em resumo, a frequência recomendada para a calibração de equipamentos varia de acordo com o tipo de equipamento, a intensidade de uso, as condições de operação e as exigências regulatórias. As empresas devem realizar uma avaliação contínua do desempenho de seus equipamentos e ajustar a frequência de calibração conforme necessário. Ao implementar práticas de calibração eficazes e regulares, as indústrias podem garantir a precisão e a confiabilidade de suas medições, contribuindo para a qualidade e a segurança de seus produtos e processos.
Erros Comuns na Calibração e Como Evitá-los
A calibração de equipamentos é um processo crítico para garantir a precisão e a confiabilidade das medições em diversos setores. No entanto, existem erros comuns que podem ocorrer durante esse processo, comprometendo a eficácia da calibração e, consequentemente, a qualidade dos produtos e serviços. Neste artigo, discutiremos alguns desses erros e como evitá-los, garantindo que a calibração seja realizada de forma eficaz.
Um dos erros mais frequentes na calibração é a falta de um padrão de referência adequado. A calibração deve ser realizada em comparação com um padrão que tenha uma precisão conhecida e que seja rastreável a padrões nacionais ou internacionais. Se o padrão utilizado não for adequado, os resultados da calibração podem ser imprecisos. Para evitar esse erro, é fundamental que as empresas utilizem padrões de referência que sejam regularmente calibrados e que atendam às normas exigidas. Além disso, é importante que os técnicos responsáveis pela calibração estejam cientes da importância de utilizar padrões confiáveis.
Outro erro comum é a calibração em condições inadequadas. A temperatura, umidade e vibrações podem afetar significativamente os resultados da calibração. Por exemplo, se um equipamento for calibrado em um ambiente com temperaturas extremas ou alta umidade, isso pode levar a medições imprecisas. Para evitar esse problema, as calibrações devem ser realizadas em ambientes controlados, onde as condições possam ser monitoradas e mantidas dentro dos limites especificados. A escolha de um local adequado para a calibração é essencial para garantir resultados precisos.
A falta de treinamento adequado dos técnicos que realizam a calibração também é um erro que pode comprometer a precisão do processo. Técnicos não treinados podem não seguir os procedimentos corretos, resultando em medições imprecisas. Para evitar esse erro, as empresas devem investir em treinamento contínuo para seus funcionários, garantindo que eles estejam atualizados sobre as melhores práticas e procedimentos de calibração. Além disso, a documentação dos processos de calibração deve ser clara e acessível, permitindo que os técnicos sigam as diretrizes estabelecidas.
Outro erro comum é a falta de documentação adequada durante o processo de calibração. A documentação é essencial para garantir que todos os passos do processo sejam registrados e que os resultados possam ser rastreados. Sem uma documentação adequada, pode ser difícil identificar problemas ou realizar auditorias. Para evitar esse erro, as empresas devem implementar um sistema de gerenciamento de documentos que inclua registros detalhados de todas as calibrações realizadas, incluindo datas, resultados e quaisquer ajustes feitos. Isso não apenas ajuda a manter a conformidade, mas também facilita a identificação de tendências e problemas ao longo do tempo.
A calibração inadequada dos instrumentos também é um erro que pode ocorrer. Isso pode incluir a calibração de um equipamento em um único ponto, em vez de em múltiplos pontos de medição. A calibração em múltiplos pontos é importante para garantir que o equipamento funcione corretamente em toda a sua faixa de operação. Para evitar esse erro, as empresas devem estabelecer procedimentos que incluam a calibração em vários pontos, especialmente para instrumentos que operam em uma ampla gama de medições. Isso ajuda a identificar desvios que podem não ser evidentes em uma única medição.
Além disso, a falta de manutenção regular dos equipamentos de calibração pode levar a erros. Equipamentos que não são mantidos adequadamente podem apresentar falhas que afetam a precisão das medições. Para evitar esse problema, as empresas devem implementar um programa de manutenção preventiva que inclua inspeções regulares e reparos conforme necessário. Isso garante que os equipamentos de calibração estejam sempre em boas condições de funcionamento e prontos para fornecer resultados precisos.
Outro erro que pode ocorrer é a pressão para realizar calibrações rapidamente, o que pode levar a descuidos e medições imprecisas. A pressa pode resultar em procedimentos sendo pulados ou realizados de forma inadequada. Para evitar esse erro, as empresas devem estabelecer prazos realistas para a calibração e garantir que os técnicos tenham tempo suficiente para realizar o trabalho corretamente. A qualidade deve ser priorizada em relação à velocidade, pois medições imprecisas podem resultar em custos muito maiores a longo prazo.
Por fim, a escolha inadequada de uma empresa de calibração de instrumentos de medição pode levar a erros significativos. É fundamental escolher um fornecedor confiável e experiente, que siga as normas e regulamentos aplicáveis. A pesquisa e a verificação de referências podem ajudar as empresas a encontrar um parceiro de calibração que atenda às suas necessidades e garanta resultados precisos.
Em resumo, a calibração de equipamentos é um processo crítico que deve ser realizado com cuidado e atenção. Erros comuns, como a falta de padrões adequados, condições inadequadas, falta de treinamento, documentação insuficiente, calibração inadequada, falta de manutenção, pressa e escolha inadequada de fornecedores podem comprometer a precisão das medições. Ao estar ciente desses erros e implementar práticas para evitá-los, as empresas podem garantir que suas calibrações sejam eficazes e que seus equipamentos operem com precisão, contribuindo para a qualidade e a segurança de seus produtos e processos.
Em conclusão, a calibração de equipamentos é uma prática essencial que não deve ser negligenciada em qualquer setor que dependa de medições precisas. Através da calibração adequada, as empresas podem garantir a qualidade de seus produtos, a segurança de seus processos e a conformidade com as normas regulatórias. Ao compreender a importância da calibração, os métodos disponíveis, a frequência necessária e os erros comuns a serem evitados, as organizações podem implementar práticas eficazes que promovam a eficiência e a confiabilidade. Investir em calibração não é apenas uma questão de conformidade, mas uma estratégia que contribui para a excelência operacional e a satisfação do cliente.