Calibração de Equipamentos é Essencial para Garantir Precisão e Confiabilidade
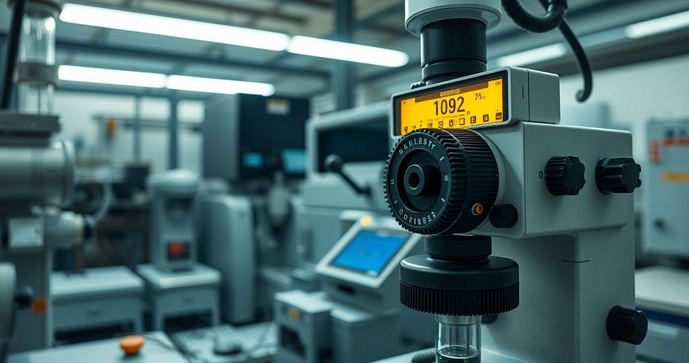
Por: Cláudio - 18 de Março de 2025
A calibração de equipamentos é um processo crucial que assegura a precisão e a confiabilidade das medições em diversos setores, como industrial, laboratorial e de pesquisa. Com a crescente demanda por qualidade e eficiência, entender a importância da calibração e os métodos adequados para realizá-la se torna essencial. Neste artigo, abordaremos os principais aspectos da calibração de equipamentos, incluindo sua importância, métodos, frequência recomendada e erros comuns a serem evitados.
Importância da Calibração de Equipamentos na Indústria
A calibração de equipamentos é um procedimento essencial na indústria, pois garante que os instrumentos de medição estejam funcionando corretamente e fornecendo resultados precisos. A precisão das medições é fundamental para a qualidade dos produtos, a segurança dos processos e a conformidade com normas regulatórias. Quando os equipamentos não estão calibrados, os resultados podem ser imprecisos, levando a decisões erradas que podem impactar negativamente a produção e a reputação da empresa.
Um dos principais motivos para a calibração de equipamentos é a manutenção da qualidade do produto. Em setores como farmacêutico, alimentício e químico, a precisão nas medições é vital. Por exemplo, em uma linha de produção de medicamentos, a dosagem correta dos ingredientes ativos é crucial para garantir a eficácia e a segurança do produto final. Se os equipamentos de medição não estiverem calibrados, isso pode resultar em produtos fora das especificações, levando a recalls, multas e danos à reputação da empresa.
Além disso, a calibração de equipamentos ajuda a garantir a segurança dos processos industriais. Equipamentos que não estão calibrados podem apresentar falhas, resultando em acidentes de trabalho e riscos à saúde dos colaboradores. Por exemplo, em indústrias que lidam com substâncias químicas perigosas, a precisão nas medições é fundamental para evitar reações indesejadas e garantir a segurança dos trabalhadores. A calibração regular dos equipamentos de medição, como balanças e sensores, é uma prática recomendada para minimizar esses riscos.
A conformidade com normas e regulamentos também é um fator importante que destaca a necessidade da calibração de equipamentos. Muitas indústrias são obrigadas a seguir normas específicas, como as estabelecidas pela ISO (Organização Internacional de Normalização) e pela ANVISA (Agência Nacional de Vigilância Sanitária). Essas normas frequentemente exigem que os equipamentos de medição sejam calibrados regularmente para garantir a precisão e a confiabilidade dos resultados. A não conformidade pode resultar em penalidades severas, incluindo a suspensão das operações e a perda de licenças.
Outro aspecto relevante é a eficiência operacional. Equipamentos calibrados corretamente tendem a operar de maneira mais eficiente, reduzindo o tempo de inatividade e os custos de manutenção. Quando os instrumentos de medição estão fora de calibração, pode haver um aumento no desperdício de materiais e tempo, já que os operadores podem precisar repetir processos ou ajustar configurações com base em medições imprecisas. A calibração regular ajuda a otimizar os processos, garantindo que os equipamentos funcionem dentro das especificações e contribuam para a produtividade geral da empresa.
Além disso, a calibração de equipamentos pode impactar diretamente a satisfação do cliente. Produtos de qualidade inferior, resultantes de medições imprecisas, podem levar a reclamações e insatisfação dos clientes. Em um mercado competitivo, a reputação de uma empresa é um ativo valioso. Garantir que os produtos atendam às expectativas dos clientes é fundamental para manter a lealdade e a confiança. A calibração de equipamentos é uma maneira eficaz de assegurar que os produtos finais atendam aos padrões de qualidade exigidos pelos consumidores.
Por fim, a calibração de equipamentos também é uma prática que promove a cultura de qualidade dentro da organização. Ao implementar um programa de calibração eficaz, as empresas demonstram seu compromisso com a qualidade e a melhoria contínua. Isso não apenas ajuda a garantir a precisão das medições, mas também incentiva os colaboradores a adotarem práticas de trabalho mais rigorosas e a se preocuparem com a qualidade em todas as etapas do processo produtivo.
Em resumo, a calibração de equipamentos na indústria é de extrema importância para garantir a qualidade do produto, a segurança dos processos, a conformidade com normas regulatórias, a eficiência operacional e a satisfação do cliente. Para empresas que utilizam balanças, por exemplo, a Calibração de balanças é uma prática essencial que deve ser realizada regularmente para assegurar a precisão nas medições. Investir na calibração de equipamentos é, portanto, um passo fundamental para o sucesso e a sustentabilidade de qualquer operação industrial.
Métodos Comuns de Calibração de Equipamentos
A calibração de equipamentos é um processo crítico que assegura a precisão e a confiabilidade das medições em diversos setores. Existem vários métodos de calibração que podem ser aplicados, dependendo do tipo de equipamento e das especificações exigidas. Neste artigo, abordaremos alguns dos métodos mais comuns de calibração de equipamentos, destacando suas características e aplicações.
Um dos métodos mais utilizados é a calibração por comparação. Este método envolve a comparação do equipamento a ser calibrado com um padrão de referência que possui uma precisão conhecida. O equipamento de referência deve ser calibrado e rastreável a padrões nacionais ou internacionais. Durante o processo, o operador realiza medições com ambos os instrumentos e compara os resultados. Se houver discrepâncias, ajustes podem ser feitos no equipamento em questão para garantir que suas medições estejam alinhadas com o padrão de referência. Este método é amplamente utilizado em laboratórios e indústrias, pois é relativamente simples e eficaz.
Outro método comum é a calibração por ajuste. Neste caso, o equipamento é ajustado diretamente para atender a um padrão específico. Isso é frequentemente utilizado em instrumentos que possuem um mecanismo de ajuste interno, como balanças e medidores de pressão. O operador realiza medições e, se os resultados não estiverem dentro das especificações, o equipamento é ajustado até que as medições estejam corretas. Este método é eficaz, mas requer que o operador tenha um bom entendimento do funcionamento do equipamento e das especificações de calibração.
A calibração por simulação é um método que utiliza um dispositivo de simulação para reproduzir as condições de operação do equipamento. Este método é particularmente útil para equipamentos que não podem ser calibrados diretamente, como instrumentos de medição de temperatura e umidade. O simulador gera sinais que imitam as condições reais, permitindo que o operador verifique se o equipamento responde corretamente. A calibração por simulação é frequentemente utilizada em laboratórios de pesquisa e desenvolvimento, onde a precisão é fundamental.
Além disso, a calibração por transferência é um método que envolve a utilização de um equipamento de referência que já foi calibrado. Neste caso, o equipamento a ser calibrado é colocado em um ambiente controlado, onde as condições de temperatura e pressão são mantidas constantes. O equipamento de referência é utilizado para medir as mesmas variáveis que o equipamento a ser calibrado. A diferença entre as medições é então utilizada para ajustar o equipamento em questão. Este método é útil para equipamentos que operam em condições específicas e requerem uma calibração precisa.
Outro método importante é a calibração de torquímetro, que é essencial para garantir a precisão em aplicações que envolvem torque. O torquímetro é um instrumento utilizado para medir a força de aperto em parafusos e porcas. A calibração deste equipamento é crucial, pois um torque inadequado pode levar a falhas em montagens e comprometer a segurança de estruturas. A Calibração de torquímetro é realizada utilizando padrões de torque conhecidos, onde o torquímetro é testado em diferentes pontos de ajuste para garantir que suas medições estejam corretas. Este processo é vital em indústrias automotivas, de construção e em qualquer aplicação onde a precisão do torque seja crítica.
A calibração de instrumentos eletrônicos, como multímetros e osciloscópios, também é um aspecto importante. Esses instrumentos são calibrados utilizando padrões de tensão, corrente e frequência. O processo geralmente envolve a aplicação de sinais de teste e a comparação das leituras do instrumento com os valores conhecidos. A calibração de equipamentos eletrônicos é essencial em ambientes de laboratório e produção, onde a precisão das medições elétricas é fundamental para a qualidade do produto final.
Além dos métodos mencionados, a calibração pode ser realizada em campo ou em laboratório. A calibração em campo é frequentemente utilizada para equipamentos que não podem ser facilmente transportados, como medidores de pressão em instalações industriais. Neste caso, os técnicos realizam a calibração no local, utilizando equipamentos de referência portáteis. Por outro lado, a calibração em laboratório permite um controle mais rigoroso das condições ambientais e é ideal para equipamentos que exigem um ambiente controlado.
Por fim, é importante ressaltar que a calibração deve ser realizada por profissionais qualificados e com experiência. A precisão das medições depende não apenas do método utilizado, mas também da habilidade do operador e da qualidade dos equipamentos de referência. Além disso, a documentação adequada do processo de calibração é fundamental para garantir a rastreabilidade e a conformidade com normas regulatórias.
Em resumo, existem diversos métodos de calibração de equipamentos, cada um com suas características e aplicações específicas. A escolha do método adequado depende do tipo de equipamento, das condições de operação e das exigências de precisão. A calibração regular é essencial para garantir a confiabilidade das medições e a qualidade dos produtos, contribuindo para a eficiência e a segurança das operações industriais.
Frequência Recomendada para Calibração de Equipamentos
A calibração de equipamentos é uma prática essencial para garantir a precisão e a confiabilidade das medições em diversos setores. No entanto, a eficácia dessa prática depende não apenas da qualidade do processo de calibração, mas também da frequência com que ela é realizada. A determinação da frequência recomendada para calibração de equipamentos pode variar de acordo com diversos fatores, incluindo o tipo de equipamento, a aplicação, as condições de operação e as exigências regulatórias.
Um dos principais fatores a serem considerados ao estabelecer a frequência de calibração é o tipo de equipamento. Equipamentos que operam em ambientes rigorosos ou que estão sujeitos a condições extremas, como temperatura, umidade e vibração, podem exigir calibrações mais frequentes. Por exemplo, instrumentos utilizados em indústrias químicas ou petroquímicas, onde há exposição a substâncias corrosivas, podem sofrer desgastes mais rapidamente e, portanto, necessitar de calibrações regulares para garantir a precisão das medições.
Além disso, a frequência de calibração pode ser influenciada pela criticidade do equipamento em relação à segurança e à qualidade do produto. Equipamentos que desempenham um papel crucial na segurança operacional, como válvulas de segurança, devem ser calibrados com mais frequência. A Calibração de válvula de segurança, por exemplo, é vital para garantir que esses dispositivos funcionem corretamente em situações de emergência. A falha de uma válvula de segurança pode resultar em acidentes graves, tornando a calibração regular uma prioridade para garantir a segurança dos trabalhadores e a integridade das instalações.
Outro aspecto a ser considerado é a frequência de uso do equipamento. Equipamentos que são utilizados com alta frequência ou que operam continuamente podem exigir calibrações mais frequentes do que aqueles que são usados esporadicamente. Por exemplo, uma balança utilizada em uma linha de produção que opera 24 horas por dia pode precisar de calibração mensal, enquanto um instrumento de medição que é utilizado apenas ocasionalmente pode ser calibrado a cada seis meses ou anualmente.
As recomendações de calibração também podem ser influenciadas por normas e regulamentos específicos do setor. Muitas indústrias são obrigadas a seguir diretrizes estabelecidas por órgãos reguladores, como a ISO (Organização Internacional de Normalização) e a ANVISA (Agência Nacional de Vigilância Sanitária). Essas normas frequentemente especificam a frequência mínima de calibração para determinados tipos de equipamentos. Portanto, é fundamental que as empresas estejam cientes das exigências regulatórias aplicáveis ao seu setor e ajustem suas práticas de calibração de acordo.
Além disso, a análise de histórico de desempenho do equipamento pode fornecer informações valiosas sobre a necessidade de calibração. Se um equipamento apresentar medições inconsistentes ou fora das especificações, isso pode indicar que a calibração deve ser realizada com mais frequência. A implementação de um programa de manutenção preditiva, que monitore o desempenho dos equipamentos ao longo do tempo, pode ajudar a identificar quando a calibração é necessária, permitindo que as empresas ajustem suas práticas de acordo com as necessidades reais.
É importante ressaltar que a calibração não deve ser vista apenas como uma obrigação, mas como uma oportunidade para melhorar a qualidade e a eficiência operacional. A calibração regular ajuda a identificar problemas potenciais antes que eles se tornem críticos, reduzindo o risco de falhas e aumentando a confiabilidade dos processos. Além disso, a calibração adequada pode resultar em economia de custos a longo prazo, evitando desperdícios e retrabalhos causados por medições imprecisas.
Por fim, a documentação adequada da calibração é fundamental para garantir a rastreabilidade e a conformidade com as normas regulatórias. As empresas devem manter registros detalhados das calibrações realizadas, incluindo datas, resultados e quaisquer ajustes feitos. Isso não apenas ajuda a garantir a conformidade, mas também fornece uma base para a análise de tendências e a tomada de decisões informadas sobre a frequência de calibração no futuro.
Em resumo, a frequência recomendada para calibração de equipamentos deve ser determinada com base em uma combinação de fatores, incluindo o tipo de equipamento, as condições de operação, a criticidade para a segurança e a qualidade do produto, a frequência de uso e as exigências regulatórias. A calibração regular é essencial para garantir a precisão das medições e a confiabilidade dos processos, contribuindo para a segurança e a eficiência operacional das empresas. Ao implementar um programa de calibração eficaz e adaptável, as organizações podem maximizar a qualidade de seus produtos e serviços, garantindo a satisfação do cliente e a conformidade com as normas do setor.
Erros Comuns na Calibração e Como Evitá-los
A calibração de equipamentos é um processo crítico que garante a precisão e a confiabilidade das medições em diversos setores. No entanto, erros podem ocorrer durante esse processo, comprometendo a eficácia da calibração e, consequentemente, a qualidade dos produtos e serviços. Neste artigo, abordaremos os erros comuns na calibração e como evitá-los, garantindo que os equipamentos funcionem de maneira adequada e eficiente.
Um dos erros mais frequentes na calibração é a falta de um padrão de referência adequado. A calibração deve ser realizada em comparação com um padrão que tenha uma precisão conhecida e que seja rastreável a normas nacionais ou internacionais. Quando um padrão inadequado é utilizado, as medições podem ser imprecisas, levando a ajustes incorretos nos equipamentos. Para evitar esse erro, é fundamental que as empresas utilizem padrões de referência calibrados e certificados, garantindo que suas medições sejam confiáveis.
Outro erro comum é a falta de treinamento adequado dos operadores responsáveis pela calibração. A calibração é um processo técnico que requer conhecimento e habilidades específicas. Operadores não treinados podem cometer erros ao realizar medições, ajustar equipamentos ou interpretar resultados. Para evitar esse problema, as empresas devem investir em treinamento contínuo para seus colaboradores, garantindo que eles estejam atualizados sobre as melhores práticas e procedimentos de calibração. Além disso, a documentação de procedimentos operacionais padrão (POPs) pode servir como um guia útil durante o processo de calibração.
A calibração em condições inadequadas também é um erro que pode comprometer os resultados. Fatores como temperatura, umidade e vibração podem afetar a precisão das medições. Por exemplo, calibrar um equipamento em um ambiente com variações extremas de temperatura pode resultar em leituras imprecisas. Para evitar esse erro, é importante realizar a calibração em um ambiente controlado, onde as condições possam ser mantidas dentro das especificações recomendadas pelo fabricante do equipamento. Isso garantirá que as medições sejam consistentes e confiáveis.
Além disso, a falta de documentação adequada durante o processo de calibração pode levar a erros. Registros incompletos ou imprecisos podem dificultar a rastreabilidade e a análise de tendências ao longo do tempo. É essencial que todas as calibrações sejam documentadas de forma detalhada, incluindo informações sobre os padrões utilizados, os resultados obtidos e quaisquer ajustes realizados. Essa documentação não apenas ajuda a garantir a conformidade com normas regulatórias, mas também fornece uma base para a melhoria contínua dos processos de calibração.
Outro erro comum é a calibração em intervalos inadequados. A frequência de calibração deve ser determinada com base em fatores como o tipo de equipamento, as condições de operação e a criticidade das medições. Calibrar equipamentos com muita frequência pode resultar em custos desnecessários, enquanto a calibração em intervalos muito longos pode levar a medições imprecisas. Para evitar esse erro, as empresas devem estabelecer um programa de calibração que leve em consideração as necessidades específicas de cada equipamento, ajustando a frequência conforme necessário.
A falta de manutenção preventiva também pode impactar negativamente a calibração. Equipamentos que não são mantidos adequadamente podem apresentar falhas que afetam a precisão das medições. Por exemplo, um sensor sujo ou danificado pode resultar em leituras incorretas. Para evitar esse problema, é importante implementar um programa de manutenção preventiva que inclua inspeções regulares e limpeza dos equipamentos. Isso garantirá que os instrumentos estejam sempre em boas condições de funcionamento e prontos para a calibração.
Além disso, a escolha inadequada do método de calibração pode levar a erros. Existem diferentes métodos de calibração, e a escolha do método mais apropriado depende do tipo de equipamento e das especificações exigidas. Utilizar um método inadequado pode resultar em medições imprecisas e ajustes incorretos. Para evitar esse erro, as empresas devem estar cientes dos métodos de calibração disponíveis e escolher aquele que melhor se adapta às suas necessidades. Consultar uma Empresa de calibração de instrumentos de medição pode ser uma boa opção para obter orientações sobre o método mais adequado.
Por fim, a falta de revisão e análise dos resultados de calibração pode levar a erros recorrentes. É importante que as empresas realizem análises periódicas dos resultados de calibração para identificar tendências e problemas potenciais. Se um equipamento apresentar medições inconsistentes, isso pode indicar a necessidade de ajustes ou manutenção. Implementar um sistema de monitoramento e análise de dados pode ajudar a identificar problemas antes que se tornem críticos, garantindo a precisão e a confiabilidade das medições.
Em resumo, a calibração de equipamentos é um processo essencial que deve ser realizado com cuidado e atenção. Erros comuns, como a falta de padrões adequados, treinamento insuficiente, condições inadequadas, documentação deficiente, calibração em intervalos inadequados, falta de manutenção preventiva, escolha inadequada do método e falta de análise de resultados, podem comprometer a eficácia da calibração. Ao estar ciente desses erros e implementar medidas para evitá-los, as empresas podem garantir que seus equipamentos funcionem de maneira precisa e confiável, contribuindo para a qualidade e a segurança de seus produtos e serviços.
Em conclusão, a calibração de equipamentos é uma prática indispensável para garantir a precisão e a confiabilidade das medições em diversos setores. A compreensão de sua importância, a escolha dos métodos adequados, a definição da frequência de calibração e a conscientização sobre os erros comuns a serem evitados são fundamentais para otimizar processos e assegurar a qualidade dos produtos e serviços. Investir em calibração não apenas melhora a eficiência operacional, mas também contribui para a segurança e a satisfação do cliente. Portanto, as empresas devem adotar uma abordagem proativa em relação à calibração, implementando práticas eficazes e buscando sempre a melhoria contínua.